PNEUMATICS
Introduction
Before the 1950's, pneumatics was most commonly used as a working medium in the form of stored energy. During the 1950's the sensing and processing roles developed in parallel with working requirements. This development enabled working operations to be controlled using sensors for the measurement of machine states and conditions. The development of sensors, processors and actuators has led to the introduction of pneumatic systems.
In parallel with the introduction of total systems, the individual elements have further developed with changes in material, manufacturing and design processes.
Pneumatics has for some considerable time been used for carrying out the simplest mechanical tasks, but in more recent times has played a more important role in the sphere of automation.
In the majority of pneumatic applications compressed air is being used for one or more of the following functions :-
to enable sensors to determine status of processes
to allow switching of actuators by using final control elements
to carry out work
Industrial Applications Employing Pneumatics
This is a small selection of applications which have become common place in modern manufacturing processes.
Methods of material handling:-
Clamping
Indexing
Positioning
Orienting
Applications:-
Packaging
Feeding
Metering
Door or chute control
Transfer of materials
Turning and inverting of parts
Sorting of parts
Stacking of components
Stamping and embossing of components
Pneumatic applications can also be used in carrying out machining and working operations. ie:-
Drilling
Turning
Milling
Sawing
Finishing
Forming
Quality control
Why Use Pneumatics?
Pneumatics have distinct advantages and distinguishing characteristics due to the utilisation of compressed air. These can be summarised as below:-
Availability: Air is available practically everywhere in unlimited quantities.
Transport: Air can be easily transported in pipelines, even over large distances.
Storage: A compressor need not be in continuous operation. Compressed air can be stored in a reservoir and removed as required. In addition, the reservoir can be transportable.
Temperature: Compressed air is relatively insensitive to temperature fluctuations. This ensures reliable operation, even under extreme conditions.
Explosion proof: Compressed air offers minimal risk of explosion or fire, hence no expensive protection against explosion is required.
Cleanliness: Unlubricated exhaust air is clean. Any unlubricated air which escapes through leaking pipes or components does not cause contamination. This is an important point when considering the food, wood and textile industries.
Components: The operating components are of simple construction and are therefore relatively inexpensive.
Speed: Compressed air is a very fast working medium. This enables high working speeds to be attained.
Adjustable: With compressed air components, speeds and forces are infinitely variable.
Overload safe: Pneumatic tools and operating components can be loaded to the point of stopping and are therefore overload safe.
In order to accurately define the areas of application of pneumatics, it is also necessary to be acquainted with the negative characteristics:
Preparation: Compressed air requires good preparation or servicing. Dirt and condensate should not be present.
Compressible: It is not always possible to achieve uniform and constant piston speeds with compressed air.
Force: Compressed air is economical only up to a certain force requirement. Under the normal working pressure of 6-7 bar (600 to 700 kPa) and dependent on the travel and speed, the output limit is between 20000 and 30000 Newtons.
Noise level: The exhaust air is loud. This problem has now, however, been largely solved due to the development of sound absorption material and silencers.
Costs: Compressed air is a relatively expensive means of conveying power. The high energy costs are partially compensated by inexpensive components and higher performance.
Factors Involved in System Design and Selection
A comparison with other forms of energy is an essential part of the selection process when considering pneumatics as a control or working medium. This evaluation embraces the total system, from the input signal (sensors) through to the control (processor), to output devices (actuators). Factors to be considered, ie :-
Work or output requirements
Preferred control methods
Resources and expertise available to support the project
Existing systems which are to be integrated with the new project
The above should be analysed and applied to the types of working and control media available, ie :-
Mechanical
Electrical / Electronic
Hydraulic
Pneumatic / Hydro-pneumatic
A combination of the above
A list of selection criteria for the working and control sections of a typical production facility are shown in Table 3.0 below
Table 3.0 Comparison of Working and Control Function Media
WORKING | CONTROL |
Force | Reliability of components |
Stroke | Sensitivity to environmental influences |
Type of motion (linear, rotary) | Ease of maintenance and repair |
Speed | Switching time of components |
Size | Signal speed |
Service life | Space requirements |
Sensitivity | Service life |
Safety and reliability | Training of operators and maintainers |
Energy costs | Modification of the control system |
Controllability | |
Handling | |
Storage |
Overview Of A Pneumatic System
A pneumatic system can be broken down into a number of levels representing hardware and signal flow.
The various levels form a control path for signal flow from the signal (input) to the work (output).
COMPONENTS OF A PNEUMATIC SYSTEM
Energy Supply
The air supply for a particular pneumatic application should be sufficient and of adequate quality.
Air is compressed to approximately 1/7th of its volume by the air compressor and delivered to an air distribution system in the factory. To ensure the quality of the air is acceptable, air service equipment is utilised to prepare the air before being applied to the control system.
Malfunctions can be considerably reduced in the system if the compressed air is correctly prepared. A number of aspects must be considered relative to air preparation :-
Quantity of air required to meet the demands of the system
Type of compressor the be used to produce the quantity required
Storage required
Requirements for air cleanliness
Acceptable humidity levels to reduce corrosion and sticky operation
Low temperature of the air and effects on the system
Pressure requirements
Line sizes and valve sizes to meet demand
Material selection and system requirements for the environment
Drainage points and exhaust outlets in the distribution system
Lubrication requirements, if necessary
Layout of the distribution system to meet demand
As a rule pneumatic components are designed for a maximum operating pressure of 8 - 10 bar (800 - 1000 kPa) but in practice it is recommended to operate at between 5 and 6 bar (500 - 600 kPa) for economic use. Due to the pressure losses in the distribution system the compressor should deliver between 6.5 and 7 bar (650 - 700 kPa) to attain these figures.
An air receiver should be fitted to reduce pressure fluctuations. In normal operation the compressor fills the receiver when required and the receiver is available as a reserve at all times. This reduces the switching cycles of the compressor. See Figure 3.13
If oil is required for the pneumatic system then this should be separately metered using air service equipment. In a normal situation, components should be selected for the control system that does not require lubrication. See Figure 3.14 for an example of an air service unit.
Compressed air filter
Compressed air regulator
Compressed air lubricator
The correct combination, size and type of these elements are determined by the application and the control system demand. An air service unit is fitted at each control system in the network to ensure the quality of air for each individual task.
Compressed air filter:-
The compressed air filter has the job of removing all contaminants from the compressed air flowing through it as well as water which has already condensed. The compressed air enters the filter bowl through guide slots. Liquid particles and larger particles of dirt are separated centrifugally collecting in the lower part of the filter bowl. The collected condensate must be drained before the level exceeds the maximum condensate mark, as it will otherwise be re-entrained in the air stream.
Compressed air regulator :-
The purpose of the regulator is to keep the operating pressure (secondary pressure) virtually constant regardless of fluctuations in the line pressure (primary pressure) and the air consumption.
Compressed air lubricator:-
The purpose of the lubricator is to deliver a metered quantity of oil mist into a leg of the air distribution system when necessary for the use by pneumatic control and working components.
Pneumatic Valves
Pneumatic Valves
Valves can be divided into a number of groups according to their function in relation to signal type, actuation method and construction. The primary function of the valve is to alter, generate or cancel signals for the purpose of sensing, processing and controlling. Additionally the valve can be used as a power valve for the supply of working air to the actuator. Therefore the following categories are relevant :-
Directional control valves
Signalling elements
Processing elements
Power elements
Non-return valves
Flow control valves
Pressure control valves
Combinational valves
Directional Control Valves
Directional control valves in particular, as their name implies, control fluid flow direction. They are applied in pneumatic circuits to provide control functions which:-
control direction of actuator motion (power valve);
select an alternative flow path (shunt valve);
perform logic control functions ("AND", "OR" functions);
stop and start flow of fluid (on - off valve);
sense machine and actuator positions (limit valves).
Directional control valves are classified according to their specific design characteristics:
1. Internal valve mechanism (internal control element) which directs the flow of the fluid. Such a mechanism can either be a poppet disc, a poppet ball, a sliding spool, a rotary plug, or a combination of poppet and spool.
2. Number of switching positions (usually two or three). Some valves may provide more than three, and in exceptional cases up to six switching positions (selector valves).
3. Number of connection ports (not called number of ways!). These ports connect the pneumatic pressure lines to the internal flow channels of the valve mechanism and often also determine the flow rate through it.
4. Method of valve actuation which causes the valve mechanism to move into an alternative switching position and return the valve to its original state.
See circuit presentation for more on valve schematic representation.
Valve Mechanisms
Directional control valves consist of a valve body or valve housing and a valve mechanism. Some valves are mounted to a sub-plate. The ports in the sub-plate or on the valve body are threaded to hold the tube fittings which connect the valve to the fluid conductor lines (tubes). Some valves have the tube fittings moulded into the valve body. This is normally the case where the valve body is made from plastic. The valve mechanism directs the pressurised fluid (compressed air) through the valve body to the selected output ports or stops the fluid from passing through the valve.
Poppet, spool, flat slide, toggle disc and spool/poppet mechanism are predominantly used in directional control valves whereas poppets and balls are the preferred mechanism in check valves and logic "OR" function and "AND" function valves.
Normally Closed And Normally Open Valves
These terms are generally applied to three port valves. The valve shown in Figure 3.15 (top) is a two position three port valve permitting no flow from pressure port 1 to output port 2 in its normal spring biased position. In the case of the normally open valve, Figure 3.15 (bottom), the supply is allowed to stream to output port 2 while the valve is in its normal position. Both valves when operated switch their flow mode to the flow configuration depicted in the left hand square of the valve symbol.

Methods Of Valve Actuation
Methods Of Valve Actuation
The term actuation in relation to pneumatic valves refers to the various methods of moving the valve mechanism into any of its alternative switching positions. Valves can be actuated by five basic methods:
manually
mechanically
electrically
hydraulically
pneumatically
In complex machine applications any of these methods, or combinations of them, may be used to gain optimum control. Manual methods use hand or foot actuators such as levers, push buttons, knobs and foot pedals, electrical methods use A.C. or D.C. solenoids. For pneumatic/electronic control integration some manufacturers make low wattage coils for direct P.L.C. connection. Solenoids range from 12 to 240 volts. Most solenoid and air pilot valves are also equipped with a manual override buttons or plungers. Thus the valve mechanism can be operated even when the air pilot signal or the electrical signal should fail. In hydraulically and pneumatically operated valves the fluid pilot signal is made to act onto a piston or it may act directly onto the valve mechanism and thus move it to its alternative position.
Spring-Actuated Valves
The terms spring-biased or spring-offset, and in the case of three-position valves spring-centred, refer to the application of springs which return the valve mechanism to its rest position as soon as the pilot signal command is cancelled. Such commands, whether they be pneumatic, electric or manual, must be maintained as long as the valve is to remain in its non-normal or actuated position.
A valve without a spring bias is actuated entirely by its external controls, and can therefore "float" or "drift" between its two extreme positions wherever the external control is cancelled. To avoid this, a "detent" mechanism or friction-producing seal rings are used to give the valve a by-stable (or memory) characteristic. Thus when the valve is switched (selected) into a specific flow condition, it will remain in that condition until switched into its alternative condition.
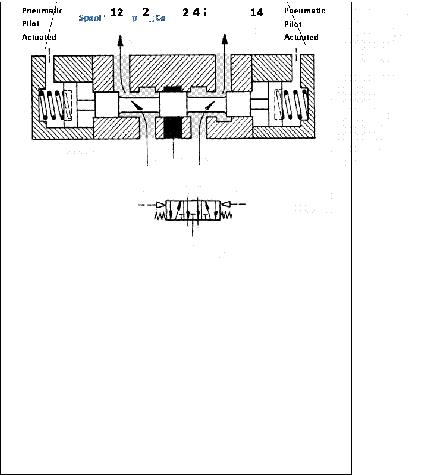

Spool Valves
In modern valve designs, the spool valve, shown in Figure 3.16, is most frequently used. Spool valves offer a number of advantages over poppet and flat-slide valves, see Figure 3.17.
* Spool valves may be used for flow reversal.
* Since flow forces acting onto the lands are equal (equal pressure on equal area) the valve is said to be balanced and uses therefore only small actuating forces.
* Spool valves may operate without elastomeric seals if the spool to body tolerance is kept small (below 0.003 mm) and fluid pressure does not exceed 900 kPa (9 bar).
* Spool valves may be built for more than two switching positions, but then the spool is normally spring centred, see Figure 3.16, or hand lever operated with detented positions.
With spool valves care must be taken to mount the valve onto a reasonably flat (preferably machined) surface, since only slight body distortion may warp the valve body sufficiently to make the closely toleranced and lapped spool seize, or hinder it from moving freely when actuated. The same may also be said for bolting the valve tool firmly against its mounting surface.
Spool valves are susceptible to contamination from poorly conditioned compressed air. Therefore close monitoring of the air quality - its filtration and lubrication is required
Flat Slide Valves
Flat slide valves are a modern adaptation of the old steam valve used on steam locomotives. The flat slide is carried to and fro by a grooved piston. See Figure 3.17. The piston may either be air-pilot signal or spring or solenoid/air pilot operated. The valve cannot be flow reversed (port 1 cannot be used as port 3 and vice versa) but it offers the advantage of a combined exhaust port which may be useful for actuator speed control. Since compressed air forces the flat slide against its bearing surface, the flat slide provides absolute leak free (pressure assisted) sealing and automatically adjusts for wear on its gliding surface. Flat slide valves are also made with a double slide to gain two exhaust ports and some valves have also snap action toggle discs instead of carrier spools.
Poppet Valves
Poppet valves offer at least two significant advantages over spool and flat slide valves.
* Poppet valves are robust and do not require lubrication. They have no close tolerance gaps on moving parts since they provide head-on instead of dynamic sealing.
* Poppet valves provide positive and air pressure assisted sealing (air pressure acts onto the underside of the poppet, See Figure 3.18
Due to the sealing design, poppet valves require a much higher operating force than any other valve design type and thus are often built with air-pilot operating assistance. The operating mechanism (roller, plunger, lever) opens a small pilot valve. This pilot valve directs pilot air to a large piston or diaphragm which operates the poppet mechanism.
True poppet valves are not flow reversible (port 1 cannot be interchanged for port 3). Hence some component manufacturers offer a poppet valve for normally open as well as for normally closed flow configuration.
Friction Free Valves (Toggle Disc Valves)
These valves are specifically designed to combine all the advantages of spool and poppet valves and at the same time eliminate all the disadvantages of spool and poppet valves. Friction free valves, as their name implies, work totally friction free and offer also the following advantages :- See Figure 3.19.
* High air flow characteristics. Equal or better than spool valves.
* Static, long life sealing. The seal ring moves head-on against the sealing lips (same as in poppet valves).
* The seal carrier (spool) is suspended between the two pre-tensioned discs and moves friction-free to and fro.
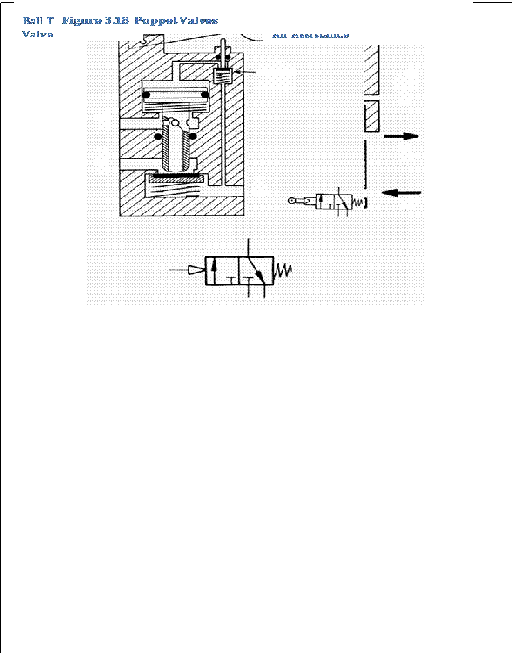
* Actuation of the disc moves it over the toggle point and tension forces snap the disc rapidly into its alternate position, thus giving rapid flow switching and memory function.
* Air contamination cannot impair valve movement and lubrication of the compressed air is not required.
* The valve is flow reversible which means port 1 may become port 3 and vice versa.
As a power element the directional control valve must deliver the required quantity or air to match the actuator requirements and hence there is a need for larger volume flow rates and therefore larger sizes. This may result in a larger supply port or manifold being used to deliver the air to the actuator.
Flow Control For Pneumatics
The flow control valve restricts or throttles the air in a particular direction to reduce the flow rate of the air and hence control the signal flow. If the flow control valve is left wide open then the flow should be almost the same as if the restrictor is not fitted. In some cases it is possible to infinitely vary the restrictor from fully open to completely closed. If the flow control valve is fitted with a non-return valve then the function of flow-control is unidirectional with full free flow in one direction. A two way restrictor restricts the air in both directions of flow and is not fitted with the non-return valve. The flow control valve should be fitted as close to the working element as is possible and must be adjusted to match the requirements of the application.
Flow control valves are frequently used in pneumatic systems. Their use is limited to the control of compressed air to and from the actuator and their main functions are :-
* to control the maximum speed of the actuator piston and its attached
load,
* to provide constant speed for the main part of the actuator piston stroke when acceleration is completed,
* to cushion the load impact at the end of the actuator stroke or decelerate a load to a lower speed,
* to prevent free falling of a heavy load on vertical movements.
Simple Restrictor Type Flow Control
This valve, being variable as far as the cross section of the orifice is concerned, is therefore also called a variable restrictor flow control valve or variable orifice flow control valve. It is mostly used on the outlet of the power valves and restricts the flow of air in both directions See Figure 3.2
Theses valves consist of a valve body and a throttling screw which adjusts the orifice cross-section to achieve the desired speed on the actuator.
Variable Restrictor With Free Reverse Flow
Where speed control (flow control) in only one valve direction is required, a check valve is built into the flow control. This permits unrestricted flow of air in the reverse direction. See Figure 3.21
The construction of this type of valve apart from the inbuilt check valve is identical to the simple restrictor type. The check valve consists of a rubber ring, which can flex upward if reverse flow is required, and a ring hub to hold the disc onto the check valve orifice during the throttling function.
Some pneumatic component manufacturers also make miniature type flow control valves which are directly built into the exhaust ports of the power valve. Others manufacture an actuator swivel-fitting which contains a small flow control valve with free reverse flow. Such inbuilt valves save space, extra connectors and installation costs.
Hydraulic Check Speed Control
Any form of pneumatic speed control no matter how effective , can never provide absolute speed consistency. See Figure 3.22. Speed consistency is imperative for machining operations or applications in manufacturing where the quality of the product depends on absolute uniform speed over the entire stroke length.
For such cases an hydraulic check cylinder may be used. The hydraulic oil, which is virtually incompressible, is used to provide precise and uniform speed control which is independent and unaffected by load variations of the pneumatic actuator. The pneumatic actuator is linked to the hydraulic check
cylinder. The force needed to move the hydraulic piston and its piston rod comes from the pneumatic actuator which literally drags the hydraulic piston along. The displaced oil is forced via a hydraulic flow control valve which provides the required speed control. An oil reservoir with a spring loaded piston compensates for the differing oil volumes displaced by the hydraulic piston and makes up for oil losses due to piston rod lubrication.
Installation Methods For Restrictor Type Flow Controls
Two basic methods are commonly used to install restrictor type flow controls. These methods are widely known as meter-in flow control and meter-out flow control. Both methods have their distinct advantages and disadvantages, but where possible meter-out should be given preference.
Meter-in speed control
Where an actuator has insufficient air volume on the exhaust side of the moving piston, so that the exhausting air cannot be sufficiently compressed by the flow control to cause an air-cushion, then meter-in speed control must be used. This is mainly the case with small diameter or short stroke actuators. Meter-in must also be used for single acting actuators.
Meter-out speed control
Meter-out provides the necessary back-pressure which is imperative for smooth and constant piston speed.
The back pressure brought about by meter-out speed control reduces the force output of the actuator, which demands that a larger piston must be selected to move the given load. The advantages gained from meter-out speed control are numerous and may be listed as :-
* A free falling. suspended or supported load can be controlled.
* The back pressure caused by a meter-out speed control resists the advancing piston which is driven forward by the pressure on the opposite side. This form of speed control provides excellent and constant control of the actuator speed.
* Pneumatic end-cushioning is greatly enhanced with the air pressure cushion caused by the meter-out speed control restrictor valve.
Power valve exhaust port speed control
To achieve optimal speed control it is advisable to mount the flow restrictors (speed control valves) directly onto the actuator.
Frequently these valves are mounted onto the exhaust ports of the power valves. With this installation, however, there is risk of damaging the pneumatic seals inside the power valve or rupturing the air hose between the actuator and the power valve. This may occur because of pressure intensification induced by an oversize piston rod.
Non Return Valves And Derivatives
The non-return valve allows a signal to flow through the device in one direction and in the other direction blocks the flow. There are many variations in construction and size derived from the basic non-return valve. Other derived valves utilise features of the non-return valve by the incorporation of non-return elements. The non-return valve can be found as an element of the one way flow control valve, quick exhaust valve, shuttle valve and the two-pressure valve.
"AND" Function Valve (two pressure valve)
Some component manufacturers make a special purpose "AND" function valve (two pressure valve). This valve ensures that both expected input signals must be present on the valve before either of them is permitted to pass through to the outlet port. The first arriving signal shifts the valve element (twin poppet), and the weaker or second arriving signal finds its way to the outlet port; thus it may be said that both input signals are required. The valve is extremely simple in its construction and costs less than an air pilot operated spool or spool/poppet valve. This type of valve is widely available and has the advantage that the weaker signal may be used as the pilot signal and the stronger signal passes through the valve. See Figure 3.23
"OR" Function Valve (shuttle valve)
Most component manufacturers make a special purpose "OR" function valve (shuttle valve). See Figure 3.24 This valve connects either input 1 or input 2 to the outlet port A, but prevents any cross flow from input 1 to input 2 or vice versa. It is to be noted that a T-connector must not be used to merge two pilot signal lines.
The pneumatic cylinder has a significant role as linear drive unit, due to its relatively low cost, ease of installation, simple and robust construction and availability in various sizes and stroke lengths.
The pneumatic cylinder has the following general characteristics:
For example:-
Diameters 6 to 320 mm
Stroke lengths 1 to 2000 mm
Available forces 2 to 50000 N
Piston speed 0.02 to 1 m/s
Pneumatic linear actuators are used to convert the stored (static) energy of compressed air into linear mechanical force or motion. Although the actuator itself produces linear motion, a variety of mechanical linkages and devices may be attached to it to produce a final output force which is rotary, semi-rotary or a combination of linear and rotary. Levers and linkages may also be attached to achieve force multiplication or force reduction as well as an increase or reduction of motion speed. Actuators can be broken down into groups:
Linear actuators
Single acting cylinder
Double acting cylinder
Rotary actuators
Vane type
Air motors
The generation of linear thrust force with a pneumatic actuator is very simple and direct. The compressed air when delivered to one end of the actuator, acts against the piston area and produces a force against the piston (force = pressure x area). The piston with the attached piston rod starts to move in linear direction as long as the reacting force is smaller. The developed force is used to move a load which may be attached either to the protruding piston rod or to the actuator housing. The distance through which the piston travels is known as the stroke.
Single acting actuators
Single acting actuators produce pneumatic force in one direction only. These actuators may be mounted in vertical direction, thus permitting the previously moved or lifted load to return the piston to its initial position. When the actuator must be mounted horizontally or when no external force can be used to return the piston, then an inbuilt spring is used to cause retraction or return of the piston.
When using a single acting actuator the force available from the air operated stroke is reduced by the opposing spring force. It must be noted that the force due to the spring compression is progressively decreasing along its stroke. Single acting actuators are usually built with a stroke length up to 100 mm.
Some manufacturers of pneumatic actuators make a special type of single acting actuator, called a short stroke clamping cylinder or diaphragm actuator. These actuators have extremely short strokes ranging from 1 to 10 mm and piston areas ranging from 100 to 3000 mm2, whereby the large piston (diaphragm) actuators normally have the extremely short strokes of 1 to 2 mm.
Such clamping actuators are normally retracted by either an inbuilt spring or by the pre-tensioned diaphragm.
Double acting actuators
Double acting actuators permit the application of pneumatic force in both stroke directions. However, the retraction stroke develops a much smaller force than the extension stroke, since the compressed air acts on a smaller area known as the annular area. See Figure 3.25
Double-ended actuators with rods protruding on both actuator ends are used where the developed force must be equal for both piston-rod movement directions (extension and retraction). Since the volumes to be filled with compressed air are equal for extension and retraction, the resulting piston speeds are also equal for both strokes. Double ended actuators provide also better piston rod guidance since loads are borne over two bearing bushes; one on each actuator end. Double ended actuators may also prove advantageous where the limit valves (position sequence valves) or electrical limit switches cannot be placed near the reciprocating piston rod. This may be the case where the transported load moves in a hostile environment, or in an area of extreme heat, or in a liquid. In such a case, the rear piston rod is used to actuate the limit valves and the front piston rod moves the load.
Pneumatic end-position cushioning (simply called cushioning) refers to the controlled deceleration of the mass in motion during its final part of the actuator stroke. The kinetic energy released on impact at the stroke end must be absorbed by the internal stroke limit stops. These stops are usually a protruding bush which is an extended part of the end caps.
For large and fast moving masses or for actuators with piston diameters above 25 mm pneumatic end-cushioning is recommended. Figure 3.26 shows a cross-section of a pneumatic cushioning mechanism built into the end caps of pneumatic actuators. The piston is fitted with a tapered cushioning bush (boss). When this bush enters into the air exit bore of the end cap (during the final part of the stroke), the main air exit begins to shut until it finally closes off completely. This first stage of exit flow throttling may cause an initial slight speed reduction. The remaining air in the annular cavity around the cushioning boss is now trapped and the momentum of the mass carries the piston on against the trapped air; thus compressing it to a high pressure. As the pressure rises, the resulting resisting force forms a cushion and begins to decelerate the piston and its mass (load)
As the kinetic energy is dispelled, the mass is slowed down to a much reduced speed which matches the rate of air flow permitted and adjusted by the cushioning valve. A check valve is also built in as part of the cushioning mechanism. This check valve allows full air flow in reverse direction to achieve fast and full force break-away from the end position.
Actuator failure
Standard type actuators are not designed to absorb piston rod side loading. Thus actuators must be mounted with care and accuracy, to ensure that the load moves precisely parallel and in alignment with the actuator centre line.
For many applications the piston rod is best fitted with a clevis or a spherical bearing rod-eye or the actuator must be allowed to swivel around a trunion mount, permitting it to swing as the direction of the load changes. A self aligning piston-rod coupling can also be used to compensate for both angular and radial misalignment, but the angular misalignment must not exceed 4 degrees in either direction and the radial alignment must not be more than 1 mm.
Failure of the rod bearing usually occurs when side load is not detected early enough or cannot be avoided. In such cases one may use a double ended piston rod type actuator or an actuator with oversize piston rod which is less flexible than a standard size piston rod.

Rodless actuators
Rodless actuators
Few pneumatic devices have enjoyed such immediate success and widespread application as the rodless actuator. An ingenious design eliminates the piston rod and cuts installation length almost to half compared to conventional double acting linear actuators. Presently, there are four design types of rodless actuators available.
Probably the most popular of these is the "Origa Rodless Cylinder". With the "ORIGA" rodless actuator principle, force from the moving piston is transferred to the carriage by means of a piston yoke that slides along the barrel slot. Its slot seal, also claiming to be absolutely free of air leaks, consists of a thin steel strip on the inside of the tube and a dust or dirt seal strip on the outside of the tube. Both steel strips pass through the piston yoke, which separates them as the piston slides along, and closes them again and forces them against a holding magnet attached to the barrel slot. The air inlet holes are located in the end-caps and so are the end-cushioning bushes. The "ORIGA" rodless actuator is extremely rigid due to its extruded type barrel construction and provides a maximum force output of 2600 newtons with a piston diameter of 80 mm at a maximum air pressure of 800 kPa (8 bar). "ORIGA" actuators are made with 80, 63 and 40 mm piston diameter and a maximum travel distance of 7000 mm See Figure 3.28.
Air Motors (Rotary Actuators)
By the use of rack and pinion drives or other mechanical systems the linear actuator (or cylinder) can be used to provide a rotary movement and so provide a torque output. Although such swivel actuators are suitable for many applications, they are not to be mistaken for air motors. Swivel actuators or semi-rotary actuators are generally built and designed to provide a rotary torque output up to a 360 degree rotation.
Air motors, however, produce a continuous torque output - thus driving a revolving drive shaft - and are regarded as the pneumatic counterpart to an electric motor. Revolving air motors are put to extremely diverse uses: from dentist's drill to the drive for a caterpillar tracked tunnel boring machine. The manufacturing industry in particular is a large user of a wide range of types and sizes of air motor driven tools such as nut runners, drills, screw drivers, grinders and sanders.
Air motors use the characteristics of compressed air power transmission to their best advantage, which means they are easily adjusted for varying speeds and torque, can be reversed, can safely be operated in an explosive environment, and can be stalled indefinitely (thus are overload safe). These
operational characteristics, combined with their excellent power features, that make air motors so versatile and widely accepted.
Air motors can be classified into five basic types, each of which produces a specific range of power output and has an operating characteristic which makes it ideally suited for a particular industrial application. These types are :-
vane motors
gear motors
piston motors
turbine motors
roots motors
In each design type the pressure exposed driving surface area must be connected mechanically to the motor output shaft. Inlet and outlet air must have a timed porting arrangement to produce continuous rotation (this feature does not apply to turbine motors).
Maximum performance varies greatly between the various design types of air motors and is determined by :-
* the ability of its internal pressure exposed areas to withstand the forces acting upon them;
* the internal leakage characteristics of the moving parts which seal the high pressure inlet from the low pressure outlet
* the efficiency of the mechanisms which link the moving pressure exposed parts to the motor drive shaft (output shaft).
Vane motors
The vane motor is the most common type of air motor used in the manufacturing industry. It covers a large range of power outputs from less than 1 kW to around 25 kW, which makes them versatile and widely accepted. See Figure 3.29 shows a cross section of a reversible vane motor. A rotor shaft which carries a number of sliding vanes is mounted eccentrically in a cylindrical casing or stator. The vanes are usually made of fibre which has excellent wear properties, and the more vanes used (up to a practical limit) the better the starting torque will be. However, increased friction from the vanes reduces efficiency.
In vane motors torque is produced by the compressed air acting onto the pressure exposed rectangular area of the vanes. These vanes in fact seal the low pressure exhaust port from the high pressure inlet port. According to Pascal's Law, which also applies to pneumatic systems, pressure acts undiminished in all directions and acts also with equal force on equal areas. It is therefore obvious that the motor shown must turn in a clockwise direction, since the sum of all vane areas being pressurised in a clockwise direction is much larger than the sum of vane areas being pressurised in an anticlockwise direction. As the rotor continues to rotate in this manner, any residual air remaining between the blades is vented via the anticlockwise supply port B. If the motor is to be operated to produce torque in the opposite direction, the anticlockwise port B is pressurised and port A is vented. The action is then exactly the reverse of that described for clockwise rotation.
As the motor turns the sliding vanes follow the contour of the cam ring (housing), thus forming sealed cavities. Since the vanes must seal and thus maintain cam ring contact at all times, and centrifugal force is absent during motor start, these vanes are usually spring loaded or air pressure loaded for smaller motors. See Figure 3.3
During motor rotation the compressed air in the pockets between the vanes is permitted to expand, since the pockets also expand as they rotate towards the exhaust opening. This permits the potential energy stored in the compressed air to be used and thus the "technical work" of the motor is increased and its efficiency is therefore also increased.
Figure 3.1 Hardware and Signal Flow
The elements in the system are represented by symbols which indicate the function of the element. The symbols can be combined to represent a solution for a particular control task using a circuit diagram. The circuit is drawn with the same structure as the signal flow diagram above. A breakdown of these primary levels can be seen in Figure 3.11.
Figure 3.11 Primary Levels of a Pneumatic System
The directional control valve (DCV) may have a sensing, a processing or an actuating control function. If the DCV is used to control a cylinder motion, then it is a control element for the actuator group. If it is used in the function of processing signals, then it is defined as a processor element. If it is used to sense motions, then it is defined as a sensor. The distinguishing feature between each of these roles is normally the method of operating the valve and where the valve is situated in the circuit diagram. This can be seen in Figure 3.12.
SYMBOLS AND STANDARDS IN PNEUMATICS
Symbols and descriptions of components
The development of pneumatic systems is assisted by a uniform approach to the representation of the elements and the circuits. The symbols used for the individual elements must display the following characteristics:
Function
Actuation and return actuation methods
Number of connections (all labelled for identification)
Number of switching positions
General operating principle
Simplified representation of the flow path
A symbol does not represent the following characteristics:
Size or dimensions of the component
Particular manufacturer, methods of construction or costs
Orientation of the ports
Any physical details of the element
Any unions or connections other than junctions
The symbols for the energy supply system can be represented as individual elements or as combined elements. The choice between using simplified or detailed symbols is dependent upon the purpose of the circuit and its complexity. In general where specific technical details are to be given such as requirements for non-lubricated air or micro-filtering, then the complete detailed symbol should be used. If a standard and common air supply is used for all components, then the simplified symbols can be used. For trouble-shooting the detailed symbols are more suitable. But the detail should not add to the complexity of the circuit for reading.
Directional control valves
The directional control valve is represented by the number of controlled connections and the number of positions. Each position is shown as a separate square. The designation of the ports is important when interpreting the circuit symbols and the valve as fitted to the physical system. To ensure that the correct lines, connections and valves are physically in place, there must be a relationship between the circuit and the components used.
Therefore all symbols on the circuit must be designated and the components used should be labelled with the correct symbol and designations. See Figure 3.32
A numbering system is used to designate directional control valves and is in accordance with ISO 5599 See Figure 3.33
Port or Connection ISO 5599
Pressure port 1
Exhaust port 3
Exhaust ports 5, 3
Signal outputs 2, 4
Pilot line opens flow 1 to 2 12
Pilot line opens flow 1 to 4 14
Pilot line flow closed 10
Methods of actuation
The methods of actuation of pneumatic directional control valves is dependent upon the requirements of the task. When applied to a directional control valve, consideration must be given to the method of initial actuation of the valve and also the method of return actuation. Normally these are two separate methods. They are both shown on the symbol either side of the position boxes. There may also be additional methods of actuation such as manual overrides, which are separately indicated.
Pressure regulating valves
Pressure regulating valves are generally adjustable against spring compression. The symbols are distinguished according to the following types:
Pressure sensing: downstream, upstream or external
Relieving or non-relieving and fluctuating pressure
Adjustable or fixed settings
The symbols represent the pressure valve as a single position valve with a flow path that is either open or closed initially. In the case of the pressure regulator the flow is always open, whereas the pressure sequence valve is closed until the pressure reaches the limit value as set on the adjustable spring. See figure 3.34
Non-return valves and derivatives
The non-return valve (check valve) is the basis for the development of many combined components. There are two main configurations for non-return valves, with and without the spring return. See figure 3.35
Flow control valves
Most flow control valves are adjustable. The one way flow control valve permits flow adjustment in one direction only with the non-return fitted. The arrow shows that the component is adjustable but does not refer to the direction of flow; it is diagrammatic only. See figure 3.35
Linear actuators
The linear actuators or cylinders are described by their type of construction and method of operation. The single acting cylinder and the double acting cylinder form the basis for design variations. The use of cushioning to reduce loads on the end caps and mountings during deceleration of the piston is important for long-life and smooth operation. The cushioning can be either fixed or adjustable. The cushioning piston is shown on the exhaust air side of the piston. The arrow indicates adjustable cushioning and not the direction of cushioned motion. See figure 3.35
Rotary actuators
Rotary actuators are divided into continuous motion and limited angle of rotation. The air motor is normally a high speed device with either fixed or adjustable speed control.
Units with limited angle of rotation are fixed or adjustable in angular displacement. The rotary actuator may be cushioned depending upon the load and speed of operation. See figure 3.36
Auxiliary symbols
There are a number of important symbols for accessories which are utilised in conjunction with pneumatics. These include the exhaust air symbols, visual indicators and the methods of connection of components. See figure 3.36
Safety requirements for pneumatic systems
There are a limited number of standards and regulations for pneumatic systems. Therefore for all factors affecting safety, reference must be made to existing general guidelines and regulations from a number of different engineering fields.
Consideration should be given to the following guidelines when operating pneumatic cylinders under clamping conditions.
The control system for the pneumatic clamping devices should be designed or arranged in such a way as to avoid accidental operation. This can be achieved by means of:
Manually-operated switching devices with protective covers
Control interlocks
Two handed operation
Precautions must be taken to prevent hand injuries caused by the clamping device. Machines with pneumatic clamping devices must be equipped in such a way that the drive of the working spindle or feed cannot be switched on until the clamping is confirmed complete. This can be achieved by checking the clamping conditions by means of:
Pressure transducers, or
Pressure sequence valves
A failure of the air supply must not cause the clamping device to open during the machining of a clamped workpiece. This can be achieved by means of:
Pressure reservoirs
Control interlocks (memory valves)
Environmental pollution
Two forms of environmental pollution may occur in pneumatic systems:
Noise: caused by the escape of compressed air
Oil mist: caused by lubricants which have been introduced at the compressor via a service unit and which are discharged into the atmosphere during the exhaust cycles.
Exhaust noise
Measures must be taken against excessive exhaust noise. This can be achieved by means of:
Exhaust silencers
Silencers are used to reduce the noise at the exhaust ports of valves. They operate on the principle of exhaust air flow control by creating a greater or lesser flow resistance. Normal silencers have only limited influence on the speed of the piston rod. In the case of throttle silencers, however, the flow resistance is adjustable. These silencers are used to control the speed of the cylinder piston rod and the valve response times. Another method of noise reduction is to fit manifolds with connections to the exhaust ports of the power valves and thus to discharge the air via a large common silencer or to return it to a reservoir.
Oil mist
The exhaust air of mechanically driven tools or mechanically controlled machines contains atomised oil which often remains in a room for some considerable time in the form of a vapour, which can be breathed in. Pollution of the environment is particularly acute in cases where a large number of air motors or large-diameter cylinders are fitted in an installation. Effective countermeasures must be taken to reduce the amount of oil mist that escapes to the atmosphere.
Operational safety
When maintaining or working with pneumatic systems, care must be taken in the removal and the reconnection of air lines. The energy stored in the tube or pipe will be expelled in a very short time with enough force to cause severe whiplash of the line which can endanger personnel. Where possible the air should be isolated at two different points, removing the air pressure before the disconnection is made. An additional danger is in the disturbance of particles due to the air blast which causes eye hazards.
CIRCUIT PRESENTATION AND CONTROL PROBLEM ANALYSIS
Recommendations for circuit array
There are no international standards for circuit presentation and layout at present, so some well proven principles are listed below:
Draw all symbols where possible in horizontal position and attach lines to the right hand square for two position valves or the centre square for three position valves
Do not mirror-invert symbols if avoidable, since this practice confuses the comprehension of signal direction, fluid-flow and valve function
Draw all valves in their de-actuated, unpressurised rest position, except for those valves which are actuated either by a lever, cam or machine part, when the machine is at rest, or at the end of a cycle. For such valves one must indicate with a cam or similar device that the valve is actuated and all attachment and pressure lines are to be connected to the left hand square.
Two-position valves which are not spring biased and can freely assume both switching positions (bi-stable valves, memory valves or detented valves) may be drawn in whatever flow-path configuration is demanded by the actuator position or initial position when the machine is at rest. But here again, the pressure lines should be connected to the right hand square for memory valves in sequential control circuits which maintain their last selected position to provide the start signal for a new machine cycle.
Where complex schematic drawings are being generated and position sensing valve signals or pressure sensing valve signals have to be distributed to a number of destinations for circuit interlocking, it is advisable to adopt the "bus-bar" distribution system, see Figure 3.38. The bus-bar should be regarded as a manifold line with both extremities closed off.
Control Problem analysis
The first step is the definition of objectives for the project with a clear definition of the problem(s). Design or development of the solution is not

involved at the analysis stage. A flow chart of the total project plan can be developed to define the step-orientated processes.
involved at the analysis stage. A flow chart of the total project plan can be developed to define the step-orientated processes.
The grouping of the total control circuit into sub-circuits seems to be one of the main difficulties which confront circuit designers. However, these obstacles can be drastically reduced by analysing the total control problem and then splitting the design into four main categories:
power circuit
sequential circuit
fringe condition modules
combinational circuit
The power circuit consists of the actuators and their directional control valves (power valves). It also includes the speed control valves and compressed air lines which connect the actuators to the power valves.
That part of the circuit which controls the stepping or sequencing of the actuators is generally called the sequential circuit. It consists of memory valves, "AND" function, "OR" function and time-delay valves.
The fringe condition circuits, which preferably are arranged in modules, affect the sequential circuit at its fringe and generally affect its start or stop characteristics (start permitted or not, emergency stop, etc.). These fringe condition modules are added in the final part of circuit deign and are designed separately.
There are two primary methods for constructing circuit diagrams:
The so-called intuitive methods, also frequently termed conventional or trial-and-error methods
The methodical design of a circuit diagram in accordance with prescribed rules and instructions
Whereas much experience and intuition is required in the first case and above all, a great deal of time where complicated circuits are concerned; designing circuit diagrams of the second category requires methodical working and a certain amount of basic theoretical knowledge.
Regardless of which method is used in developing the circuit diagram, the aim is to end up with a properly functioning and reliable operating control. Importance is now attached to operational reliability and ease of maintenance by a clear layout and documentation. Regardless of which method and which technique is used to produce a circuit diagram, fundamental knowledge of the devices concerned and a knowledge of the switching characteristics of these devices, is required