Topics in this page
1. Compressed air preparation
2. Basic Pneumatics
3. Electro-pneumatic4. Pneumatic Cylinders
5. Pneumatic complete Lecture note
6.Pneumatic tutorial problems7.1.Industrial application of pneumatics
Supplier List
pneumatic valves
pneumatics cylinders
pneumatics actuators
pneumatics connectors
pneumatics books
1. Compressed air preparation.
Pneumatics uses air to transfer energy
1. What is air?
Gas | Volume % | Weight % |
nitrogen | 78,08 | 75,51 |
oxygen | 20,95 | 23,01 |
carbon dioxide | 0,03 | 0,04 |
hydrogen | 0,01 | 0,001 |
argon | 0,93 | 1,286 |
helium | 0,0005 | 0,00007 |
neon | 0,0018 | 0,0012 |
crypton | 0,0001 | 0,0003 |
xenon | 0,0000 | 0,00004 |
Additionally: dust & vapour
2. Average content of dust in air
region | average concentration (mg/m3) | widespread particle-size (mm) | biggest particle (mm) |
country | |||
- while raining | 0,05 | 0,80 | 4,00 |
- while dryness | 0,15 | 2,00 | 25,00 |
big city | |||
- residential area | 0,40 | 7,00 | 60,00 |
- industrial area | 0,75 | 20,00 | 100,00 |
industrial area | |||
- workshop | 1 to 10 | > 60,00 | >1000,00 |
- foundry | 50 to 100 | ||
- cement factory | 100 to 200 | ||
- smoke stack | 1000 to 15000 |
3. Dust in industrial districts
field of dimension (mm) | average dimension (mm) | pieces per m2 (x 1000) | part of weight (%) |
0 to 0,5 | 0,25 | 910000 | 1 |
0,5 to 1 | 0,75 | 67000 | 2 |
1 to 3 | 2,00 | 10700 | 6 |
3 to 5 | 4,00 | 2500 | 11 |
5 to 10 | 7,50 | 1750 | 52 |
10 to 30 | 20,00 | 50 | 28 |
4. Equipment to be considered in the generation and preparation of compressed air
Þ Air compressor
Þ Air reservoir
Þ Air filter
Þ Air dryer
Þ Air lubricator
Þ Pressure regulator
Þ Drainage points
Þ Oil separators
Note: The location of compressor influences to a greater or lesser degree the amount of contamination
Types of main contamination in compressed air
Þ solids (dust)
Þ water
Þ oil
Interaction of contaminants
Þ dust combine with water or oil to form lager particles
Þ water combines with oil to form emulsions
Compressed air should be properly prepared to prevent malfunction |
Results of poorly-prepared air:
Þ pipework contamination and damage: flow-rate decreases, rust of iron, oxidation of copper
Þ valves and machinery damage: rapid wear of seals and moving parts
Þ contamination of silencer: Reduced flow through control valve, slowing down of actuators
Þ icing of valves: expanded air is cooling down - moisture freezes
Þ moisture precipitates: corrosion and wash out or initial grease, may hardening seals
Þ oiled-up valves: oil blocks bore for pilot air, switching function is impaired causes valve malfunction, may cause seal swelling, contamination of process e.g. food industry, paint spraying,
5. Drying of air
The atmospheric air taken in by the compressor always contains a proportion of moisture
The higher the air temperature, the greater the quantity of water vapour which can be take up by the air.
If the saturation point of 100% is reached, the water is precipitated in the form of droplets
How much water can be carried by air?
°C | g/m3 | °C | g/m3 |
1 | 5,15 | 26 | 24,38 |
2 | 5,52 | 27 | 25,78 |
3 | 5,92 | 28 | 27,22 |
4 | 6,35 | 29 | 28,77 |
5 | 6,80 | 30 | 30,36 |
6 | 7,28 | 31 | 32,02 |
7 | 7,77 | 32 | 33,78 |
8 | 8,29 | 33 | 35,64 |
9 | 8,84 | 34 | 37,57 |
10 | 9,40 | 35 | 39,60 |
11 | 9,99 | 36 | 41,72 |
12 | 10,65 | 37 | 43,91 |
13 | 11,35 | 38 | 46,20 |
14 | 12,07 | 39 | 48,62 |
15 | 12,82 | 40 | 51,14 |
16 | 13,63 | 41 | 53,76 |
17 | 14,48 | 42 | 56,49 |
18 | 15,37 | 43 | 59,35 |
19 | 16,32 | 44 | 62,34 |
20 | 17,29 | 45 | 65,44 |
21 | 18,31 | 46 | 68,63 |
22 | 19,38 | 47 | 71,92 |
23 | 20,53 | 48 | 75,40 |
24 | 21,74 | 49 | 79,08 |
25 | 23,04 | 50 | 82,98 |
100% of saturation at 1 bar:
Compressing the air means reduction in volume, compressed air cannot carry as much water as atmospheric air!
Example:
1. Compressor is working at 20 °C and delivers 10 m3/h, air humidity is 50%
amount of water in the air per hour: 100% saturation at 20 °C: 17,3 g/m3
m = 0.5 x 17,3 g/m3 x 10 m3/h = 86,5 g/h
2. Compressor is compressing the air at an absolute pressure of 7 bar and the temperature of the air rises to 40 °C.
Volume of the air: V = 10 m3/h / 7 = 1.43 m3/h
100% saturation at 40 °C: 51,14 g/m3
amount of water in the compressed air per hour: m = 51,14 g/m3 x 1,43 m3/h = 73,1 g/h
3. Precipitated amount of condensate entering the pneumatic system
m = 86,5 g/h - 73,13 g/h = 13,4 g/h
4. Air cools down on the way to the machinery, Temperature inside the plant 20 °C:
100% saturation at 20 °C: 17,29 g/m3
maximum amount of water in the compressed air at 20 °C:
m = 17,29 g/m3 x 1,43 m3/h = 24,7 g/h
precipitated amount of condensate: m = 73,1 g/h - 24,7 g/h = 48,4 g/h
Example
1. Compressor 10 m3/h, at 40 °C, 85% humidity
Amount of water in air: m = ?
2. Absolute pressure 8 bar, air temperature rises to 80 °C
Maximum amount of water in compressed air: m = ?
3. Air cools down on 20 °C
Amount of water in compressed air: m = ?
Amount of precipitated water: m = ?
6. Three different methods for drying air:
Low temperature drying (refrigeration)
dew point temperature about + 2 °C
Adsorption drying
dew point temperature up to - 90 °C
Membrane dryer (absorption drying)
dew point temperature up to - 40 °C
The lower the temperature dew point the more water will be reduced from the air
7. Description of different systems:
7.1 Low temperature drying
Compressed air with a temperature of about 30°C (compressor with re-cooler) gets into inlet A. Over an heat-exchanger B the air comes into the cooling-unit C. Air is cooled down to about 0°C. Water falls out D. Then the cold air goes back to the heat-exchanger an is warmed up by incoming warm air. Outlet temperature is about 20°C; Pressure dew point normally +3° to +5°C.
7.2 Adsorption drying
Compressed air with a temperature of about 30°C (compressor with re-cooler) gets into inlet A. First the air have to pass a switching valve B.
Then the air gets into drying chamber 1. By outlet point C a small part of dry air (about 15-20%) as taken to dry chamber 2.(Cold regeneration). In chamber 1 vapour is taken by an granulate.
This can be:
- molecular sieve Na AlO2 SiO2 (used by FESTO-dryer)
- active aluminium oxide Al2O3
- silica gel SiO2
When the switching valve B changes the ports from chamber 1 to chamber 2 the volume from chamber 1 goes quickly out over an air-silencer. 90% of the humidity goes to the surrounding area. Rest of 10% humidity is dried by dry air.
Regenerating time about 2 minutes.
7.3 Membrane drying
Wet air flows trough the microfilter 1 (separate to order) and gets clean into the entry A of the drying unit 2. Further the air flows through the fibre membranes 3 and the water vapour will pass through the membrane wall due the differences of partial pressures. After the water vapour passes through it is necessary to remove the water vapour from the outside area to keep the vapour pressure low. This is done by taking 10% to 30% of the dry air ( B-4-5-C) and purging it back over the outside of the membrane. The wet air goes out over a silencer 6 to the surrounding area.
8. Filtering of air
available types:
Filter element | Filter size (mm) | Residual oil in air (mg/m3) |
Sinter cartridge | 40 | - |
Sinter cartridge | 5 | - |
Micro filter | 1 | < 0,5 |
Fine filter | 0,01 | < 0,01 |
Charcoal filter | 0,003 | < 0,003 |
Function of service unit with sinter or micro filter element:
The compressed air passes through a baffle plate in the filter bowl. The air is rotated, and the heavier dust particles and water droplets are spun by centrifugal force against the inner wall of the filter bowl and run down the wall of the housing. The air which has been precleaned then passes through the filter element.
Function of service unit with charcoal filter element:
The filter element consists out of a highly porous charcoal element. The charcoal itself has a enormous effective surface. Even gaseous air contaminants like oil vapour and fumes are absorbed within by the charcoal.
9. Quality classes of compressed air
Class | Particle size mm | Particle density mg/m3 | pressure dew point °C | maximal oil content mg/m3 |
1 | 0.1 | 0.1 | -70 | 0.01 |
2 | 1 | 1 | -40 | 0.1 |
3 | 5 | 5 | -20 | 1.0 |
4 | 15 | 8 | +3 | 5 |
5 | 40 | 10 | +7 | 25 |
6 | not specified | not specified | +10 | not specified |
7 | not specified | not specified | not defined | not specified |
10. Recommended ISO-classes for some applications
Solid | Water-Dew Point | max. Oil rate | ||||
Application | Class | [mm] | Class | [°C] | Class | [mg/m3] |
Mining | 5 | 40 | 7 | - | 5 | 25 |
Cleaning | 5 | 40 | 6 | + 10 | 4 | 5 |
Welding Machinery | 5 | 40 | 6 | + 10 | 5 | 25 |
Tool Machinery | 5 | 40 | 4 | + 3 | 5 | 25 |
Compressed Air Cylinder | 5 | 40 | 4 | + 3 | 5 | 25 |
Compressed Air Valve | 3 to 5 | 5 to 40 | 4 | + 3 | 5 | 25 |
Packing | 5 | 40 | 4 | + 3 | 3 | 1 |
High precision pressure reg. | 3 | 5 | 4 | + 3 | 3 | 1 |
Air for measurement | 2 | 1 | 4 | + 3 | 3 | 1 |
Bearing air | 2 | 1 | 3 | - 20 | 3 | 1 |
Sensors | 2 | 1 | 2 to 3 | - 40 to- 20 | 2 | 0,1 |
Food | 2 | 1 | 4 | + 3 | 1 | 0,01 |
Photographic processing | 1 | 0,01 to , 0,1 | 2 | - 40 | 1 | 0,01 |
Note:
The recommended max. water contend will vary with the intended use of the compressed air. For instrument air it is often stated that the pressure dew point should be 10°C below the lowest expected site temperature.
The recommended max. water contend will vary with the intended use of the compressed air. For instrument air it is often stated that the pressure dew point should be 10°C below the lowest expected site temperature.
How can we reach recommended ISO-classes?
Compressor and Air Reservoir Pre-filter Refrigerator dryer ISO-classes
4.6.5
4.5.4
4.4.4
3.4.4
3.3.4
3.3.3
2.2.2
1.1.2
1.1.1
Adsorption dryer Microfilter Charcoal-Fine-filter
Overview about preparation methods
Solids:
Þ Cyclone separator, baffle-plate separators for particles > 15 mm (Filter bowl with baffle plate)
Þ Sintered filters (metal or polymer) for particles > 5 mm (Sintered filters 40 mm or 5 mm)
Þ Fibre filters for particles > 1 mm (Fine filter LFMA)
Þ Micro fibre filters for particles > 0,01 mm (Micro filter LFMB)
Water:
Þ Condensation and separation (cooling of air)
Þ Absorption drying (Air dryer LDF)
Þ Adsorption (membrane filters LD)
Þ Cyclone separator and filters (only for water in liquid sate, filter bowl with baffle plate)
Oil:
Þ Fibre filters for oil content > 0,5 mg/m3 (liquid or aerosol form, fine filter LFMA)
Þ Micro fibre filters for oil content > 0,01 mg/m3 (micro filter LFMB)
Þ Charcoal filters for oil vapour and odours (charcoal filter LFMPX)
How do our service units fit into this?
Type | Quality classes | ||
Solids | Water | Oil | |
FRC- | 5 | - | - |
FRC-5M- | 3 | - | - |
LFR- | 5 | - | - |
LFR-5M- | 3 | - | - |
LF- | 5 | - | - |
LF-5M- | 3 | - | - |
LFMB- | 2 | - | 4 |
LFMA- | 1 | - | 2 |
LFMPX- | 1 | - | 1 |
LD- | - | 2/3 | - |
LDF- | - | 1 | - |
Note: Since our service units are only equipped with a cyclone separator, no statement can be made regarding water content.
Mounting of service units
Þ The flow direction of each element has to be in the same direction (observe arrows on elements )
Þ Observe the consecutive order of the elements
Þ Mounting of service unit should be as close as possible to machinery
Þ Service units have to be mounted horizontally
Þ After mounting to the machinery the service unit should be visible and easy accessible for operation
2. Basic Pneumatics
Physical Properties of air
The surface of the globe is entirely covered by a mantle of air.
Air is a mixture out of the following gases:
Gas | Volume % | Weight % |
nitrogen | 78,08 | 75,51 |
oxygen | 20,95 | 23,01 |
carbon dioxide | 0,03 | 0,04 |
hydrogen | 0,01 | 0,001 |
argon | 0,93 | 1,286 |
helium | 0,0005 | 0,00007 |
neon | 0,0018 | 0,0012 |
krypton | 0,0001 | 0,0003 |
xenon | 0,0000 | 0,00004 |
The following terms and units are required for definitions in pneumatics:
Unit | Symbol | Units and unit symbol |
Length | L | Meter (m) |
Mass | m | Kilogram (kg) |
Time | t | Second (s) |
Temperature | T | Kelvin (K) |
Derived Quantities
Unit | Symbol | Units and unit symbol |
Force | F | Newton (N) = 1 Kg*m/s2 |
Area | A | Square meter (m2) |
Volume | V | Cubic meter (m3) |
Flowrate | Q | (m3/s) |
Pressure | p | Pascal (Pa) 1 Pa = 1 N/m2 1 bar = 105 Pa |
Since everything on earth is subjected to the absolute atmospheric pressure (pat), this pressure cannot be felt. The prevailing atmospheric pressure is therefore regarded as the base and any deviation is termed pg (gauge pressure).
A pressure of pg = 3 bar is a pressure which is 3 bar above the atmospheric pressure.
A pressure of pg = -0.5 bar is a pressure which is 0.5 below the atmospheric pressure.
Is the pressure compared to the zero point (a room with absolutely no air inside is without any pressure) it is termed as absolute pressure pabs.
The atmospheric pressure does not have a constant value. It varies with the geographic location and the weather. Within the international measuring system pat is therefore defined as pat = 1,013 bar (standardised atmospheric pressure).
The international unit for pressure is Pascal (Pa).
1 Pa = 1 N/m2
In pneumatics the more common unit for pressure is bar.
1 bar = 10 N/cm2
Thus the conversion between bar and Pascal is as following:
1 Pa = 10-5 bar
1 bar = 105 Pa
What is force?
Law of Newton:
Force = Mass x Acceleration |
F Force (Newton)
m Mass (Kg)
a Acceleration (m/s2)
The acceleration on earth due to the gravity is g = 9.81 m/s2 » 10 m/s2.
Example: On a box with a mass of 50 Kg acts a force of 490.5 N.
Characteristics of Pneumatic Systems
Pneumatics has for some considerable time been used for carrying out the simple mechanical tasks. Linear, swivel and rotary motions can be easily performed with pneumatic components. Especially pneumatic cylinders have a significant role as linear drive units due to their relatively low cost, ease of installation, simplicity and robust construction.
Pneumatics is competing with two other working media:
- Electrics
- Hydraulics
Advantages of pneumatic systems:
Availability: Air is available practically everywhere in unlimited quantities
Transport: Air can be easily transported in pipelines, even over large distances
Storage: Air can be stored in a reservoir and removed as required
Temperature: Compressed air is insensitive to temperature fluctuations
Explosion proof: Compressed air offers minimal risk of explosion of fire
Cleanness: Unlubricated exhaust air is clean. Leaking pipes or components cause no contamination to the environment.
Components: The operating components are of simple construction and relatively inexpensive
Speed: Compressed air is a very fast working medium.
Adjustable: Speed and forces are infinitely adjustable
Overload safe: Pneumatic tools and components can be loaded to the point of stopping without damage.
Disadvantages of pneumatic systems:
Preparation: Compressed air requires good preparation. Dirt and condensate has to be removed.
Compressibility: Air is compressible and therefore it is not always possible to achieve uniform motions or constant speeds.
Force: Compressed air is most economical at a working pressure of 6-7 bar. This limits the achievable forces. (Festo’s largest cylinder DGP-320 has a thrust of ~50.000 N at 6 bar).
Noise level: Exhausting air is loud. Using sound absorbing silencer can solve the problem.
Cost: Compressed air is a relatively expensive medium. The high energy costs are partially compensated by inexpensive components.
Air Generation and Distribution
Equipment to be considered in the generation and preparation of compressed air
1 Air Compressor
2 Recooler
3 Water and oil separator
4 Air Reservoir
5 Drainage Point
6 Air Dryer
7 Air filter and pressure regulator
Note: The location of compressor influences to a greater or lesser degree the amount of contamination
Types of main contamination in compressed air
· solids (dust)
· water
· oil
Interaction of contaminants
· dust combine with water or oil to form lager particles
· water combines with oil to form emulsions
Compressed air should be properly prepared to prevent malfunction |
Results of poorly-prepared air:
· pipe-work contamination and damage: flow-rate decreases, rust of iron, oxidation of copper
· valves and machinery damage: rapid wear of seals and moving parts
· contamination of silencer: Reduced flow through control valve, slowing down of actuators
· icing of valves: expanded air is cooling down - moisture freezes
· moisture precipitates: corrosion and wash out or initial grease, may hardening seals
· oiled-up valves: oil blocks bore for pilot air, switching function is impaired causes valve malfunction, may cause seal swelling, contamination of process e.g. food industry, paint spraying, etc.
The atmospheric air taken in by the compressor always contains a proportion of moisture. The higher the air temperature, the greater the quantity of water vapour which can be take up by the air. If the saturation point of 100% is reached, the water is precipitated in the form of droplets
How much water can be carried by air?
100% of saturation at 1 bar:
°C | g/m3 | °C | g/m3 |
1 | 5,15 | 26 | 24,38 |
2 | 5,52 | 27 | 25,78 |
3 | 5,92 | 28 | 27,22 |
4 | 6,35 | 29 | 28,77 |
5 | 6,80 | 30 | 30,36 |
6 | 7,28 | 31 | 32,02 |
7 | 7,77 | 32 | 33,78 |
8 | 8,29 | 33 | 35,64 |
9 | 8,84 | 34 | 37,57 |
10 | 9,40 | 35 | 39,60 |
11 | 9,99 | 36 | 41,72 |
12 | 10,65 | 37 | 43,91 |
13 | 11,35 | 38 | 46,20 |
14 | 12,07 | 39 | 48,62 |
15 | 12,82 | 40 | 51,14 |
16 | 13,63 | 41 | 53,76 |
17 | 14,48 | 42 | 56,49 |
18 | 15,37 | 43 | 59,35 |
19 | 16,32 | 44 | 62,34 |
20 | 17,29 | 45 | 65,44 |
21 | 18,31 | 46 | 68,63 |
22 | 19,38 | 47 | 71,92 |
23 | 20,53 | 48 | 75,40 |
24 | 21,74 | 49 | 79,08 |
25 | 23,04 | 50 | 82,98 |
Compressing the air means reduction in volume. With less volume, compressed air cannot carry as much water as uncompressed air!
Result: During the compression of air a considerable amount of water is condesating. Water separator and drainage points are essential components after the compressor stage.
Air compressor
There are a large number of different types of compressors available, with most of the compressors on the market employing one of two operating principles: The piston compressor and the screw compressor.
How does it work?
Powered by an electric motor, the pistons of the compressor are moved back and forth. The movement of the pistons creates an underpressure at the inlet end and air is sucked in. The air is forced into the second chamber via a cooling coil. The pressure is intensified in accordance with the ratio between the surface areas and the air compressed correspondingly.
How does it work?
A pair of meshing screws transports sucked-in air from the inlet end to the discharge end. The air is compressed by the tapering of the gap between the spindles. At the inlet end the spindles are wider and this enlargement of the gap causes the air to be sucked in.
Type | Advantages | Disadvantages |
Reciprocating piston compressor Single- and double-acting, single- and multi-stage, oil-free and oil-lubricated | Very suitable for high pressures Large pressure control range Good regulation characteristics Very familiar, accordingly repairs by own personnel are often possible | Not smooth-running due to oscillating mass forces High maintenance costs due to wear on pistons and cylinders High compression end temperature |
Screw compressor Single- and multi-stage, air- and water-cooled oil-free and oil-lubricated | Smooth-running Low maintenance costs Low wear Low residual oil content with oil-injected versions | High power consumption Limited pressure and control range Compressor elements require maintenance and overhaul by manufacturer |
Cooling of the compressed air leads to condensate forming which of course has to be removed from the air stream. The so-called cyclone separator is used for this purpose and is installed downstream of the recooler. The compressed air carrying droplets of moisture and aerosols flows over a swirler, which creates a rotating air stream. Centrifugal force presses the heavier droplets against the sides of the cyclone after which they flow down to collect in the condensate trap at the bottom.
Air Dryers
Low temperature drying
Compressed air with a temperature of about 30°C (compressor with re-cooler) gets into inlet A. Over an heat-exchanger B the air comes into the cooling-unit C. There the Air is cooled down to about 0°C. Water falls out D. Then the cold air goes back to the heat-exchanger an is warmed up by incoming warm air. Outlet temperature is about 20°C; Pressure dew point normally +3° to +5°C.
Adsorption drying
Compressed air with a temperature of about 30°C (compressor with re-cooler) gets into inlet A. First the air have to pass a switching valve B. Then the air gets into drying chamber 1. By outlet point C a small part of dry air (about 15-20%) as taken to dry chamber 2.(Cold regeneration). In chamber 1 vapour is taken by an granulate.
This can be:
- Molecular sieve NaAlO2 SiO2 (used by FESTO-dryer)
- Active aluminium oxideAl2O3
- Silica gel SiO2
When the switching valve B changes the ports from chamber 1 to chamber 2 the volume from chamber 1 goes quickly out over an air-silencer. 90% of the humidity goes to the surrounding area. Rest of 10% humidity is dried by dry air. Regenerating time about 2 minutes.
Membrane drying
Wet air flows trough the microfilter 1 (separate to order) and gets clean into the entry A of the drying unit 2. Further the air flows through the fibre membranes 3 and the water vapour will pass through the membrane wall due the differences of partial pressures. After the water vapour passes through it is necessary to remove the water vapour from the outside area to keep the vapour pressure low. This is done by taking 10% to 30% of the dry air (B-4-5-C) and purging it back over the outside of the membrane. The wet air goes out over a silencer 6 to the surrounding area.
Air Filter
Available types:
Filter element | Filter size (mm) | Residual oil in air (mg/m3) |
Sinter cartridge | 40 | - |
Sinter cartridge | 5 | - |
Micro filter | 1 | < 0,5 |
Fine filter | 0,01 | < 0,01 |
Charcoal filter | 0,003 | < 0,003 |
Function of service unit with sinter or micro filter element:
The compressed air passes through a baffle plate in the filter bowl. The air is rotated, and the heavier dust particles and water droplets are spun by centrifugal force against the inner wall of the filter bowl and run down the wall of the housing. The air which has been precleaned then passes through the filter element.
Function of service unit with charcoal filter element:
The filter element consists out of a highly porous charcoal element. The charcoal itself has a enormous effective surface. Even gaseous air contaminants like oil vapour and fumes are absorbed within by the charcoal.
Quality classes of compressed air
Class | Particle size mm | Particle density mg/m3 | pressure dew point °C | maximal oil content mg/m3 |
1 | 0.1 | 0.1 | -70 | 0.01 |
2 | 1 | 1 | -40 | 0.1 |
3 | 5 | 5 | -20 | 1.0 |
4 | 15 | 8 | +3 | 5 |
5 | 40 | 10 | +7 | 25 |
6 | not specified | not specified | +10 | not specified |
7 | not specified | not specified | not defined | not specified |
Air Lubricator
Today’s modern pneumatic components come with a lifetime grease package and are designed to run without additional lubrication. Nevertheless in some cases lubrication of the compressed air is desirable or even necessary.
Lubrication of compressed air is necessary for:
- fast cylinder speeds (v > 1m/s)
- rapid oscillating motions
- cylinder of large diameter (d> 125mm)
- when lubrication has been used before
Note: If a cylinder has once been operated with lubricated air, lubrication is always needed, as additional oil flushes out the basic lubrication. |
Mist lubricator
How does it work?
Compressed air is passing through a venturi nozzle in the lubricator head, creating a vacuum in the drip chamber. At the same time the oil reservoir is pressured through a check valve. The resulting pressure difference forces the oil upwards through the rise into the viaduct where it drips into a nozzle. The orifice of the nozzle is adjustable and the number of oil drops per minute can be easily counted. The drops fall through the duct into the air stream where the oil is atomised resulting in a fine oil mist.
A piece of white cardboard can be used to check the level of lubrication. At the point in the system, which is the furthest from the lubricator the cardboard is held at a distance of approximately 20 cm form a exhaust port. After the system has operated for some time, the oil mist should be seen as a pale yellow colour on the cardboard. Dripping oil is a clear sign of over-lubrication.
Pressure Regulator
Pressure regulators ensure a constant supply pressure (secondary pressure) irrespective of the pressure fluctuations in the main loop (primary pressure).
How does it work?
The operation of a pressure regulator can be divided in three different stages:
1. The output pressure acts on one side of a diaphragm and a spring acts on the other side. The spring force can be adjusted by means of a knurled screw. When output pressure P2 is less than input pressure P1 the spring pushes the diaphragm up an the valve stem opens. Compressed air is flowing in to the system.
2. When the output pressure increases, the diaphragm moves against the spring force causing the valve to close. Further rise in output pressure P2 is now stopped. P2 remains steady until air is exhausted from the secondary side (e.g. cylinder is moving) of the regulator. In this case the valve opens again and new air flows into the system (see No. 1)
3. If the pressure on the secondary side increases considerably, for example during cylinder load changes, the diaphragm is pressed against the spring. The centrepiece of the diaphragm opens and compressed air can exhaust to the atmosphere through vent holes in the regulator housing. After the overpressure is relieved, the orifice in the diaphragm is closed again.
The pressure regulator can be adjusted between the limits zero an the supply pressure. However, for best regulation characteristics, the input pressure should be always 1 bar above the desired output pressure.
Air filter, pressure regulator and lubricator are often combined in a single unit, the so-called air service unit. A service unit should be located as close as possible to the compressed air consuming
device.
The following recommendations regarding air quality are given for standard pneumatic components:
Humidity: Pressure dew point up to 10 °C
Temperature: Higher than the dew point of the compressed air, lower than the maximum
permitted ambient temperature.
Solids: Particle size up to 40 mm
Lubrication: Festo pneumatic cylinders have been already given a basic lubrication from the
factory, thus they can be operated with unlubricated as well as lubricated air.
Directional control valves
Directional control valves influence the path taken by an air stream. The directional control valve is characterised by its number of controlled ports and by the number of switching positions. Additional information is given to define the methods of actuation to achieve the different switching positions. The construction of the valve is important when analysing the flow characteristics like flow rate, maximum pressure and switching times for a particular application.
The following design principles are utilised:
Poppet valves:
- Ball valve
- Disc seat valve
Slide valves:
- Plate slide valve
- Longitudinal slide valve
2/2-way valve
A 2/2-way valve has two ports, an inlet port (1) and an outlet port (2). In one switching position the valve is closed and no air can flow from inlet to outlet port. In the other switching position the valve is open, allowing a flow of air through the valve.
2/2-way valves are simple in design and mostly used as on/off valves.
On the right side a hand lever operated 2/2-way ball valve is shown.
3/2-way valve
A 3/2-way valve has three ports and two switching positions. The valve is available in normally closed and normally open configuration.
Normally closed 3/2-way ball seat valve
In the not actuated position the valve exhaust the working port (2) to the atmosphere, while the supply port (1) is closed. When the valve is actuated, the supply air is connected to the output port (2) and the exhaust port is closed.
Normally open 3/2-way disc seat valve
In the not actuated position the air supply at port (1) is connected to the working outlet port (2). Once actuated the air supply (1) is closed and the air from working port (2) empties through exhaust port (3).
- Pneumatic push button
- Pneumatic limit switch
- Control of a single acting cylinder
4/2-way valve
A 4/2-way valve has 4 ports: One supply port (1), one exhaust port (3) and two working ports (4) and (2). Furthermore the valve has two switching positions.
The 4/2-way disc seat valve is not actuated. The supply air is connected to the working port (2) while the air from working port (4) is exhausting to the atmosphere trough port (3).
When the two plungers are actuated simultaneously, the connections (1) to (2) and (4) to (3) are closed by the first movement. By pressing the valve plungers further against the discs, the passages between (1) and (4) and (2) to (3) are opened.
The valve has no overlapping between the two switching positions and is returned to its start position by the springs. 4/2-way valves are used to control double acting cylinders.
5/2-way valve
5/2-way valves have 5 connecting ports and two working positions. Basically a 5/2-way valve has the same functionality as a 4/2-way valve. The difference between the two valves is that the 5/2-way valve has a separat exhaust port for each working port. Working port (4) exhausts through port (5) while working port (2) exhausts through port (3). Today 4/2-way valves are generally replaced by 5/2-way valves.
5/2-way suspended disc seat valve, pilot air operated
The 5/2-way valve is not actuated. The supply air is connected to the working port (2) while the air from working port (4) is exhausting to the atmosphere trough port (5).
When the valve stem is switch to the working position, the connections (1) to (2) and (4) to (5) are closed and the passages between (1) and (4) and (2) to (3) are opened. The valve has small overlapping between the two switching positions where all five ports are shortly connected together. In normal operation this overlapping is not recognized.
The ports (12) and (14) are pilot air signals, which switch the valve stem. When pilot signal (12) is applied, the valve switches to the position where (1) is connected to (2), while pilot signal (14) would switch the valve to the position where (1) is connected to (4). When both pilots are applied, the valve remains in its current switching position.
5/2-way valve with applied pilot signal (14) 5/2-way valve with applied pilot signal (12)
5/3-way valve
A 5/3-way valve has 5 ports and three switching positions. Beside the two switching positions of a standard 5/2-way valve, the 5/3-way valve has an additional mid-position. This position is reached when both pilot signals (12) and (14) are not present.
5/3-way valves come in three different designs for the mid-position:
5/3-way longitudinal slide valve mid-position closed
Mid-position: All valve ports are closed
Pilot (12) applied: Port (1) is connected to port (2) while port (4) exhausts through port (5)
Pilot (14) applied: Port (1) is connected to port (4) while port (2) exhausts through port (3)
Pilot operated valves
To avoid high actuating force, mechanically controlled valves can be equipped with an internal pilot valve to assist valve switching. This allows for example large bore valves to be operated with small actuating forces. This increases the sensitivity of the system.
How does it work?
A small hole connects the pressure connection (1) and the pilot valve. If the roller lever is operated, the pilot valve opens. Compressed air flows to the servo piston and actuates the main valve disc. First the connection from port (2) to port (3) is closed. Second the disc seat of the main valve opens, allowing the air to flow from pressure supply port (1) to working port (2).
The air supply for the pilot valve is either internally connected to the supply port (1) or supplied through a separate port (mostly numbered 12 or 14). External pilot air supply has to be chosen in the following cases:
- Valve is operated with a pressure less than approximately 3 bar
- Valve is operated with vacuum
- Flow path is used bi-directional
External pilot is recommended in the following cases:
- System incorporates a slow pressure build-up valve (soft-start)
- Compressed air is heavily lubricated (tap-off of dry air before lubricator for control purpose)
For proper valve operation the pilot air has to be correctly exhausted. Pilot exhaust ports use the numbers (82) or (84).
Symbols and description of components
The following characteristics have to be displayed:
· Function
· number of connections
· number of switching positions
· Actuation and return actuation
· simplified representation of the flow path
A symbol does not present the following characteristics:
· Size or dimension of component
· construction and design
· orientation of ports
· any physical detail of the element
The symbols used in pneumatics are detailed in the standard DIN ISO 1219 ‘’Circuit symbols for fluidic equipment and systems’’.
Valve symbols are comprised out of the following basics
From these basic the symbol for a valve is comprised. The connections are always drawn to the box, which shows the initial position.
Examples:
Actuation methods
The method of actuation of pneumatic directional control valves is dependent upon requirements of the task. The types of actuation vary in mechanical, pneumatic, electrical and combined actuation. The symbols for the methods of actuation are specified in ISO 1219.
Beside the method of actuation, the method of return actuation must also be taken in consideration. Both are shown in the symbol on either side of the position boxes.
Supply and exhaust ports
Supply of compressed air is indicated by a triangle. The exhaust of a valve can be ducted (exhaust port with thread) or unducted (exhaust is just a bore)
A numbering system is used to designate the ports of directional control valves.
Port or Connection | ISO 5599 | Lettering System (old) |
Pressure port | 1 | P |
Exhaust ports | 5, 3 | R, S |
Working ports | 4, 2 | A, B |
Pilot line opens flow 1 to 2 | 12 | Z |
Pilot line opens flow 1 to 4 | 14 | Y |
Pilot line closes flow | 10 | Z, Y |
Auxiliary pilot air | 81, 82 | Pz |
Pilot air exhaust | 83, 84 |
Examples:
Logic and flow control valves
Non return valve (Check valve)
Non return valves can stop the flow completely in one direction. In the opposite direction the flow is free with a minimal pressure drop due to the resistance of the valve. The one-way blocking action can be effected by cones, balls, plates or diaphragms.
Pilot operated non return valve
Unlike the standard non return valve, which allows flow in only one direction, the pilot operate non return valve allows an flow opposite to the blocking direction when a pilot signal (21) is applied.
If the entering pressure at connection P is higher that the outgoing pressure at A, the check valve allows the flow to pass freely. Otherwise, the valve stops the flow. Additionally, the check valve can be opened via the control line (21). This action allows the flow to pass freely in both directions.
Two pressure valve (AND)
Compressed air flows through the valve only if signals are applied at both inlets (X) and (Y).
The two pressure valve is switched based on the compressed air entering into both input connections (X) and (Y). Only one input signal blocks the flow through the valve. If signals are applied to both (X) an (Y), the signal which is last applied passes on to the outlet (A).
Shuttle valve (OR)
Compressed air flows through the valve if a signal is applied at one of its inlets (X) and (Y).
If compressed air is applied to the first inlet, the ball inside the valve seals the opposing inlet and a signal is generated at the outlet (A). Should both input connections begin receiving compressed air, the connection with the higher pressure takes precedence passes on to the outlet. When the air flow is reversed (e.g. cylinder is exhausting), the ball remains in its previously assumed position.
Quick exhaust valve
Quick exhaust valves are used to increase piston speed of cylinders. The valve allows a cylinder to extend or retract at its maximum speed by reducing the low resistance in the exhaust path. To reduce flow resistance the air is expelled to atmosphere close to the cylinder via a large orifice.
The valve has supply connection (P), an outlet (A) and an exhaust port (R). When flow direction through the valve is from (P) to (A) the air passes freely to (A) while the disc blocks exhaust port (R). However if air flow is in the opposite direction the disc seals port (P) and the air is quickly expelled to atmosphere.
Flow control valve
Flow control valves influence the volumetric flow of compressed air. The valves are normally adjustable and the setting can be locked in position. Flow control valves are used to regualte the speed of actuators. They should be fitted as close as possible to the cylinder.
Throttle valve
A throttle valve regulates the speed equally in both flow directions.
One way flow control valve
The one-way flow control valve is made up of a throttle valve and a check valve. With this type of valve the air flow is throttled in only one direction. The check valve stops the flow of air in the bypass an air can flow only through the throttle orifice. In the opposite direction, air can pass freely through the opened check valve.
Throttling circuits for double acting cylinders
For double acting cylinders, two throttling principles can be distinguished:
Supply air throttling
The air entering the cylinder is throttled. Exhaust air from the cylinder by-passes the throttle and can escape freely. Main disadvantage of this throttling system is that the slightest fluctuations in load on the piston rod lead to irregularities in the speed (stick-slip effect). Supply air throttling is only useful for single acting or small volume cylinders.
Exhaust air throttling
With exhaust air throttling, the supply air flows freely to the cylinder and the exhaust air from the cylinder is throttled. This creates a state where the piston is loaded between two cushion of air - on one side the supply pressure and on the other side the exhaust air being restricted by the throttle. The exhaust air has to pass the throttling orifice since the check valve closes the bypass.
Exhaust air throttling improves the motion behaviour of cylinders at low speeds. It is the only recommended way of throttling for double acting cylinders.
Pneumatic actuators
A pneumatic actuator is designed for converting pressure energy into useful work (motion). They can be divided into the following groups:
Single acting cylinder
With single acting cylinders compressed air is applied on only one side of the piston face. Therefore the cylinder can generate work in only one direction. The return movement of the piston is effected by a built-in spring or by the application of an external force.
For single acting cylinders with built-in spring, the stroke is limited by the natural length of the spring. The construction and simplicity of operation makes single acting cylinders particular suitable for compact, short stroke cylinders in the following types of applications:
- Clamping of work-pieces
- Cutting operation
- Ejecting parts
- Pressing operation
- Feeding and lifting
Advantages of single acting cylinders
- simple design
- less air consumption than double acting cylinder
- no lip seal at piston rod required
Disadvantages of single acting cylinders
- limited stroke due to natural length of the spring
- work force only in one direction
- work force gets less the more the rod is advancing (problem for long strokes)
Double acting
A double acting cylinder is operated by the reciprocal input of compressed air. When compressed air is applied to the rear port of the cylinder while the other side is open to the atmosphere, the cylinder starts to advance. To return the piston to its initial position the air supply has to be connected to the front port while the rear chamber of the cylinder has to be exhausted. The switching of air is done by means of a directional control valve.
Pneumatic end cushioning
If large masses are moved by a cylinder, cushioning is used in the end positions. Before reaching the end position, a cushioning piston interrupts the direct flow of air to the exhaust port. The remaining air is forced to flow through a flow control valve. Therefore the speed of the piston is slowed down for the last part of the stroke to reduce impact on the cylinder cap.
The amount of cushioning has to be adjusted by means of the flow control valve according to the maximum load the cylinder will carry.
Position sensing
Cylinders can be fitted with a magnet in the piston. This allows a contactless sensing of the position of the piston with proximity switches.
Further special designs of double acting cylinders includes:
- Square piston rod
- Double ended piston rod
- Heat resistant seals
- Flat cylinder (square piston)
- Stainless steel cylinder
- Multi position cylinder
- Tandem cylinder
- Rodless cylinder
What is force?
Law of Newton:
Force = Mass x Acceleration |
F Force (Newton)
m Mass (Kg)
a Acceleration (m/s2)
The acceleration on earth due to the gravity is g = 9.81 m/s2 » 10 m/s2.
Example: On a box with a mass of 50 Kg acts a force of 490.5 N.
Cylinder piston force
The theoretically available force is derived from the working pressure and the respective effective piston surface area. This available force is reduced by the proportion of system friction; generally, system friction amounts to between 5 and 10 % of the theoretically available force. The system friction is expressed through the efficiency factor.
The theoretical piston force is calculated as the following:
Force = Effective piston area x operating pressure x Efficiency |
A Effective piston area (m2)
p Operation pressure (Pa)
h Efficiency factor
Example:
Cylinder diameter d1 = 100 mm
Piston rod diameter d2 = 25 mm
Pressure pe = 6 bar
Efficiency factor h = 0.85
1. Effective area for advance stroke:
Aa = d12 x p /4 = (100 mm)2 x p /4 = 7853 mm2 = 78.5 cm2
2. Force for advance stroke:
Fa = p x Aa x h = 60 N/cm2 x 78.5 cm2 x 0.85 = 4003.5 N
3. Effective area for return stroke:
Ar = (d12 x p/4) - (d22 x p/4) = ((100 mm)2 x p/4) - ((25mm)2 x p/4) = 7363.1 mm2 = 73.6 cm2
4. Force for return stroke
Fr = p x Ar x h = 60 N/cm2 x 73.6 cm2 x 0.85 = 3753.6 N
Note: A double acting cylinder has on its advance stroke a greater force than on its return stroke. This is due to different effective piston areas for. For the return stroke the area of the rod has to be subtracted form the area of the piston to get the effective area.
Exercise:
Cylinder diameter d1 = 63 mm
Piston rod diameter d2 = 20 mm
Pressure pe = 6 bar
Efficiency factor h = 0.9
What is the piston force for advance and return stroke?
Designation of symbols in control diagrams:
The design of pneumatic control circuits is defined in VDI 3226. All elements are drawn in their initial positions. The actuating devices with their final control elements are located on top of the drawing. The processing elements and the input elements are located below. All Elements are designated from the top to the bottom.
Designation of Elements
Cylinder | 1.0 | 2.0 | 3.0 |
Final Control Element | 1.1 | 2.1 | 3.1 |
Input Element even numbering for extracting* | 1.2 | 2.2 | 3.2 |
odd numbering for retracting* | 1.3 | 2.3 | 3.3 |
*Internal Festo designation, not according to VDI 3226 |
For further signal or processing elements the numbering is continued in the same order.
Some elements e.g. roller lever valves may be actuated in their initial position. This is indicated by a cam, which actuates the roller lever of the valve.
Note: The position of limit switches is marked in the control diagram.
Introduction to the STEP-Diagram
For a quick overview of the functional steps of a control circuit, a displacement step diagram is used. It displays the cylinder movements in a graphical manner. It also includes information about the input signals, which trigger a certain movement.
Example I
Extraction of the double acting cylinder is started by pressing the push button 1.2. After the cylinder has reached its front position the roller leaver valve 1.3 switches the main control valve 1.1 back to its initial position and the cylinder is reversing. The cycle can be restarted, when the cylinder has been completely retracted.
STEP-Diagram
Example II
The extraction of the cylinder can be started by the actuation of the push button 2.2 or the foot lever valve 2.4. The movement can only be started, when the cylinder is in its initial position, which is sensed by the roller lever valve 2.6. After reaching its front position the roller leaver valve 2.3 switches the final control valve 2.1 back to its initial position and the cylinder is retracting
STEP-Diagram
3. Electro-pneumatic Supplier List 1 Fundamentals of control1.1 The control chainEach control system is comprised out of three discrete sections:- Output devices and their drivers - Processing elements (store the control program) - Input devices The control chain is characterised by a signal flow from signal input via processing to signal output. - placement of components in the circuit diagram - identification of physical size, current or voltage rating of components - to determine the layout of the control cabinet/console - locating of components for maintenance and service 1.2 System structureThe components of an electropneumatic system can be identified as belonging to one of the three basic groups of a control chain.Examples for assignment of devices to the three control levels in electropneumatics: Additionally there is a fourth group in the system structure, which is the energy supply. For the pneumatic parts the energy supply is an air compressor while for the electrical part the energy supply is presented through a generator, the mains, a battery or the power supply. 2 System Components2.1 Power SupplyThese are available in various configurations with different levels of filtering and regulation of the output voltage.The power supply should be able to comfortably manage the total system current requirements without overloading. Consideration should be also given to the impact of future expansion of the system. 2.2 Air supply systemThe air supply for a particular pneumatic application should be sufficient and of adequate quality.Aspects of consideration in preparation of air supply: - type of compressor to be used to produce the quantity required - storage requirements - requirements for air filtration - acceptable humidity levels to reduce corrosion and sticky operations - lubrication requirements if necessary - pressure requirements - line sizes to meet demand - drainage points and exhaust outlets in the distribution system - layout of the distribution system to meet demand Service unit Malfunction can be considerably reduced in the system if the compressed air is correctly prepared. The air service unit is a combination of the following elements: - air filter with water separator - air pressure regulator - air lubricator 3 Input Elements3.1 PNP/NPN configurationGenerally two sensor designs are distinguished, PNP (positive switching) and NPN (negative switching). PNP In case of PNP sensors, the output is connected to the positive potential in the switched state. This means one connection of the load must be connected to the proximity sensor output and the other connection to 0V. NPN In case of NPN sensors, the output is connected to the negative potential (0V) in the switched state. This means one connection of the load must be connected to the proximity sensor output and the other connection to the positive potential (e.g. 24 V). 3.2 Pressure switchA pressure switch senses the air pressure of the air-line and compares this with a pre-set adjustable value. When the pressure reaches the pre-set limit the internal changeover contacts are switched and an electrical output signal is given.Pressure switches have always a hysteresis, which prevents the output signal from flickering. On some switches the hysteresis is also adjustable. 3.3 Reed switchesReed switches are also known as magnetically actuated switches. They are commonly used to sense the position of a piston within a pneumatic cylinder. The contacts close when the switch is exposed to a magnetic field, e.g. that of a permanent magnet of a cylinder piston.Reed switches are chracterized by their small size and fast switching time. However high currents or short circuits easily destroy them. Therefore they should be never used to switch directly a solenoid valve. 3.4 Inductive sensorOperating principle The most important components of an inductive proximity sensor are an oscillator, a demodulator and an amplifier with an output stage. When supply voltage to the sensor is switch on, the oscillator starts and a defined current is flowing. If an electrically conductive object is introduced into the active zone of the sensor, eddy currents are created, which draw energy from the oscillator. This leads to a change in current consumption of the oscillator. The two statuses of current consumption are electronically evaluated to create a switching in the output stage. Inductive sensors are available in flush and non-flush fitting. Where sensors are to be flush mounted in a metal fixture, the flush-fitting type has to be selected. The non flush-fitting type requires a free-zone around the active area to avoid false switching due to the surrounding metal. However non flush-fitting sensors can be flush fitted in electrically non-conductive material like wood or plastics. Different sensing material leads to a change of the effective switching distance. Reduction factors for different materials are listed below: Reduction Factors for different materials
3.5 Capacitive SensorsThe operating principle is based on the measurement of the change of electrical capacitance of a capacitor in a RC resonate circuit. If an object or medium (metal, plastic, glass, wood, water) is introduced into the active zone, the capacitance of the resonant circuit is altered. This results in a change of the output stage of the sensor. The sensitivity (switching distance) depends not only on the distance of the medium from the active surface. It also depends on the thickness and kind of medium detected. Furthermore, most capacitive sensors have a potentiometer to adjust the sensitivity. This allows suppressing the detection of certain media. For instance, it is possible to determine the fluid level of water through the wall of a bottle. Reduction factors for different materials
3.6 Optical sensorOptical sensors use red or infrared light for the detection of objects. Each type of sensor basically consists out of two main units: the emitter and the receiver. Emitter and receiver are either installed in a common housing (diffuse, retro-reflective types) or housed separately (through-beam type). The emitter LED sends a light beam, which can be diverted, focussed, interrupted or reflected. The phototransistor of the receiver accepts the light, separates external light influences and electronically evaluates the optical signal.To suppress the influence from external light sources, the light beam on an optical sensor in modulated. Red light makes it easier to adjust the sensor, since it is visible in contrast to the infrared light. On the other hand infrared light can span greater distances and is less susceptible to interference from ambient light. Variants of optical proximity sensors Through-beam sensors Through-beam sensors consist of separately assembled emitter and receiver. To trigger the sensor output signal, the cross section of the light beam must be covered by an object. The object should permit only minimum penetration of light, but may reflect any amount of light. - Large switching range possible ( up to 100m) - Small objects can be detected (especially with fibre optic cable) - Objects can be diffuse reflecting, mirroring or low translucent - Good positioning accuracy Disadvantages of through-beam sensors - Two separate modules - Can’t be used for completely transparent objects Retro-reflective sensors Light emitter and light receiver are installed in a single housing. An additional reflector is required. To trigger the sensor output signal an object must interrupt the light beam between sensor and reflector. This interruption must not be compensated by direct or diffuse reflection of the object. Transparent, bright or shiny objects may remain undetected. - Simple installation and adjustment - Offers larger switching range in comparison to diffuse sensors Disadvantages of retro-reflective sensors - Transparent, very bright or shiny objects remain undetected Diffuse Sensors Advantages of diffuse sensors - No additional reflector required - The object can be diffuse reflecting, mirroring or transparent to translucent as long as a sufficiently high percentage of the light beam is definitely reflected. - Diffuse sensor allow frontal detection, i.e. in the direction of the light beam Disadvantages of diffuse sensors - Not suitable if accurate lateral response is crucial Correction factors taken into account for different object surfaces
3.7 Switches and relaysSwitches are primarily distinguished by their contact configuration - normally open (path 3 to 4) - normally closed (path 1 to 2) - changeover contacts (path 1 to 2 or 1 to 4) On actuation a normally open (NO) contact enables energy flow while a normally closed contact (NC) disables energy flow. The changeover contacts (CO) can be used as either normally open or normally closed contacts or both. Contact configuration Switches may consist of a single pair of contacts either normally open (NO) or normally closed (NC) or have a set of changeover (CO) contacts. More complex configurations (multi-pole switches) are available. A range of actuation methods is also available such as pushbutton, mechanical electrical or pneumatic actuation. The actuation method can be momentary (non-latching) or detented (latching), Important considerations when selecting switches include - Current and voltage rating of contacts - Level of electrical insulation of the switch housing - Number and configuration of contacts - Method of actuation and switch design Most switches including relays use a numbering system to identify their contacts. Additionally the whole switch can be identified (e.g. switch number one, two,...). Contact numbering system In electropneumatics relay are generally used as signal processors. Rather than switching a solenoid directly via a limit switch or electric sensor, the relay contacts act as a buffer, carrying the larger amount of current. Relay characteristics - A small amount of energy applied to the relay coil can control a larger energy flow through the relay contact - Relays are able to switch a number of independent circuit paths - Isolate the input signal (relay coil) from the output signal (relay contacts). This is refereed to be a potential free contact. - High operating speed, i.e. short switching times. 4 Actuating devicessolenoid valvesSolenoid principle If a conductor is formed into the shape of a coil and current is passing through the conductor, an electromotive force is generated. By adding turns to the conductor, the magnetic field is strengthened and adding turns to the conductor increases the force. Adding an iron core to the solenoid further increases the force. DC solenoid When current is applied to the solenoid head, a magnetic field is generated which influences the valve stem and the soft iron core at the end of the stem housing. The divers polarities at the soft iron core and the valve stem initiates a force of attraction, which causes the stem to be pulled up. When the current is switched off, the magnetic field collapses and the spring pushes back the stem into its initial position. When the solenoid is switched on, the current rises slowly. During development of the magnetic field the inductance of the coil generates a force which opposes the applied voltage. This explains the slightly slow energising action of DC solenoid. Switching off solenoids When inductive devices such as solenoids are switched off, the magnetic field collapses. This can result in an induced voltage peak, which is many times higher than the normal coil voltage. This voltage peak causes arcing across switches and relay contacts resulting in increased wear of the contact material. Electronic devices such as proximity sensors or transistor outputs o PLCs can be seriously damaged. To protect electronic devices and to reduce the increased contact wear of switches, an arc suppression circuit is fit in parallel to the solenoid. The use of the following elements is possible: - Arc quencher - Zener diode - R-C combination Illuminated seals fit between socket and solenoid and contain additionally two arc quencher diodes. Comparison between DC and AC solenoids
4.2 Advantage: Short switching time for pneumatic output Disadvantage: High force needed to operate the valve stem. This would require large solenoids 4.3 Pilot operated solenoid valveThe pilot valve can be considered an amplifier. By using pilot control, the size of the solenoid can be kept to a minimum. This has two main advantages:- reduced power consumption - reduced heat generation Single/double solenoid valves Unlike valves with a spring return the double solenoid valve remains in its last switching position, even with power removed from both solenoids, until an opposing signal is applied. This means the valve has memory characteristics. For electropneumatic circuits this characteristics has several advantages: - only short duration of electrical signal necessary to switch the valve - demand on the electrical power supply can be minimised - in case of electrical power loss the valve will not switch back, thus preventing uncontrolled cylinder movements Application example for single solenoid valves - pneumatic press - shut of f pneumatic supply when E-stop button is pressed - saves one output on a PLC controller compared to double solenoid valve Application example for double solenoid valve - clamping of workpiece during processing - shorter overall switching time (spring return is 40ms compared to 15ms with solenoid) - applications where energy saving or reduced heat generation is important 4.4 Pneumatic cylinderIf a cylinder moves large masses, cushioning is used in the end positions. Before reaching the end position, a cushioning piston interrupts the direct flow of air to the outside. The air is forced to flow through flow control valve. Therefore the speed of the piston is slowed down for the last part of the stroke to reduce impact on the cylinder. Other features · Pneumatic end position damping is adjustable via two regular screws. · The Piston of the cylinder can be fitted with a permanent magnet which can be used to operate a proximity switch for position sensing · Cylinder barrel is usually made from seamless drawn steel tubing and can be coated to withstand harsh environments. · Piston rod is preferably made form heat-treated, rust-proofed type of steel. · The two caps are fastened to the cylinder barrel by tie rods · The seals are made from either Perbunan (up to +80 °C), Viton (up to +190°C) or Teflon (up to +200 °C) Rotary actuator 5 Electropneumatic symbolsSymbols should identify and clearly represent the following characteristics of components:- function - labelling of connections - actuation methods - number of switching positions - simplified representation of flow/current path Symbols do not represent - construction method or manufacturer - component dimension or energy handling capability - orientation of valve/cylinder ports or electrical connection - physical details of element 5.1 Most important electrical symbols:5.2 Most important pneumatic symbols for electropneumatic6 System DevelopmentEach electropneumatic circuit can be divided in two distinctive parts- pneumatics - electrical There exists an interface between the pneumatic and electrical elements. These elements will appear on both the pneumatic and electrical circuit diagrams. The steps in development of a basic circuit - Describe operation of circuit - Develop a displacement step diagram for the pneumatic actuators - Draw the pneumatic circuit - Specify the pneumatic/electric interface - Draw the electrical diagram - Document maintenance information (numbering and designation of elements) - Document type of components and technical data Development guide for pneumatics - circuit layout should follow the signal flow through the control chain from bottom to top - cylinders and directional control valves are drawn horizontally with the cylinders operating from left to right. Numbering of pneumatic circuit elements is done the following way
- layout should follow the signal flow through the control chain (input, processing, output) from top to bottom - circuits with relay control can be further divided into a control section and a power section - components should be placed from left to right according to the sequence of operation Example for electrical layout Electrical circuit elements are numbered, following the direction of signal flow from top to bottom and from left to right. Often elements are also given the number of the rung in which they appear as well as the number of the page on which they are drawn. Electrical elements in the circuit drawing are illustrated in the initial position. If a switch is operated (e.g. limit switch) it is drawn in operation (NO drawn as NC and NC drawn as NO) which is afterwards indicated by an arrow Example of actuated proximity sensor and limit switch 6.1 Link between pneumatics and electric layouts |
· Pneumatic end position damping is adjustable via two regular screws.
· The Piston of the cylinder can be fitted with a permanent magnet which can be used to operate a proximity switch for position sensing
· Cylinder barrel is usually made from seamless drawn steel tubing and can be coated to withstand harsh environments.
· Piston rod is preferably made form heat-treated, rust-proofed type of steel.
· The two caps are fastened to the cylinder barrel by tie rods
· The seals are made from either Perbunan (up to +80 °C), Viton (up to +190°C) or Teflon (up
to +200 °C)
2. What is pressure?
The surface of the globe is entirely covered by a mantle of air.The following terms and units are required for definitions in pneumatics:
Unit | Symbol | Units and unit symbol |
Length | L | Meter (m) |
Mass | m | Kilogram (kg) |
Time | t | Second (s) |
Temperature | T | Kelvin (K) |
Unit | Symbol | Units and unit symbol |
Force | F | Newton (N) = 1 Kg*m/s2 |
Area | A | Square meter (m2) |
Volume | V | Cubic meter (m3) |
Flowrate | Q | (m3/s) |
Pressure | p | Pascal (Pa) 1 Pa = 1 N/m2 1 bar = 105 Pa |
A pressure of pe = 3 bar is a pressure which is 3 bar above the atmospheric pressure.
A pressure of pe = -0.5 bar is a pressure which is 0.5 below the atmospheric pressure.
Is the pressure compared to the zero point (a room with absolutely no air inside is without any pressure) it is termed as absolute pressure pabs.
The international unit for pressure is Pascal (Pa).
1 Pa = 1 N/m2
In pneumatics the more common unit for pressure is bar.
1 bar = 10 N/cm2
Thus the conversion between bar and Pascal is as following:
1 Pa = 10-5 bar
1 bar = 105 Pa
3. What is force?
Law of Newton:Force = Mass x Acceleration |
m Mass (Kg)
a Acceleration (m/s2)
The acceleration on earth due to the gravity is g = 9.81 m/s2 » 10 m/s2.
Example: On a box with a mass of 50 Kg acts a force of 490.5 N.
4. Cylinder piston force
The theoretically available force is derived from the working pressure and the respective effective piston surface area. This available force is reduced by the proportion of system friction; generally, system friction amounts to between 5 and 10 % of the theoretically available force. The system friction is expressed through the efficiency factor.The theoretical piston force is calculated as the following:
Force = Effective piston area x operating pressure x Efficiency |
p Operation pressure (Pa)
h Efficiency factor
Example:
Cylinder diameter d1 = 100 mm
Piston rod diameter d2 = 25 mm
Pressure pe = 6 bar
Efficiency factor h = 0.85
1. Effective area for advance stroke:
Aa = d12 x p /4 = (100 mm)2 x p /4 = 7853 mm2 = 78.5 cm2
2. Force for advance stroke:
Fa = p x Aa x h = 60 N/cm2 x 78.5 cm2 x 0.85 = 4003.5 N
3. Effective area for return stroke:
Ar = (d12 x p/4) - (d22 x p/4) = ((100 mm)2 x p/4) - ((25mm)2 x p/4) = 7363.1 mm2 = 73.6 cm2
4. Force for return stroke
Fr = p x Ar x h = 60 N/cm2 x 73.6 cm2 x 0.85 = 3753.6 N
Note: A double acting cylinder has on its advance stroke a greater force than on its return stroke. This is due to different effective piston areas for. For the return stroke the area of the rod has to be subtracted form the area of the piston to get the effective area.
Exercise:
Cylinder diameter d1 = 63 mm
Piston rod diameter d2 = 20 mm
Pressure pe = 6 bar
Efficiency factor h = 0.9
What is the piston force for advance and return stroke?
Theoretically available force in N at p = 6 bar
Piston [mm] | 32 | 40 | 50 | 63 | 80 | 100 | 125 | 160 | 200 | 250 | 320 |
Piston rod [mm] | 12 | 16 | 20 | 20 | 25 | 25 | 32 | 40 | 40 | 50 | 63 |
Advancing | 483 | 754 | 1178 | 1870 | 3016 | 4712 | 7363 | 12064 | 18850 | 29452 | 48255 |
Retracting | 415 | 633 686 | 990 1056 | 1682 1750 | 2721 2847 | 4418 | 6881 | 11310 11110 | 18096 17895 | 28274 | 46385 |
Important: In order to ensure a high service life and sufficient force to accelerate the piston, the cylinder should not be loaded with more than 80% of its theoretical piston force! |
A cardbox with a mass of 30 Kg has to be lifted vertically by a pneumatic cylinder. The supply pressure is 6 bar. What cylinder size (diameter) has to be selected when the utilisation factor of the cylinder should not exceed 80% ? It is supposed that there is no friction in the cylinder.
1. What force is necessary to lift the cardbox?
Fg = m x g = 30 kg x 10 m/s2 = 300 N
2. What effective piston area is necessary (at 6 bar) to lift the cardbox?
F = p x A
A = F/p = 300 N / 60 N/cm2 = 5 cm2
3. Select cylinder diameter
A = d2 x p/4
Since there is no cylinder with a diameter of 25.2 mm the next available size has to be selected.
Selected cylinder size: 32 mm
4. Control of utilisation factor:
Theoretical piston force for diameter 32 mm at 6 bar: Fth = 483 N (see table)
Utilisation = 100 x Fg/Fth = 100 x 300 N/483N = 62.1 %
The utilisation factor is not exceeded!
Exercise:
A pneumatic cylinder is used to lift an oil barrel on a ramp (see sketch). The mass of a full barrel is 150 Kg. The supply pressure is 6 bar. What cylinder size (diameter) has to be selected when the utilisation factor of the cylinder should not exceed 80% ? It is supposed that there is no friction in the cylinder.
5. Cylinder air consumption
For the preparation of the air and to obtain facts concerning the costs, it is important to know the air consumption of a system.The air consumption depends on operation pressure, piston diameter and stroke length. It is calculated by the following formula:
Q = |
A1 Effective piston area advance stroke (cm2)
A2 Effective piston area return stroke (cm2)
s Piston stroke (cm)
n Cycles per minute
pat atmospheric pressure (bar)
pe operating pressure (bar)
Example:
Double acting cylinder with d = 50 mm (piston rod diameter = 20 mm)
Stroke length s = 100 mm
Operating pressure pe = 6 bar
Cycles: n = 20 1/min
Atmospheric pressure pat = 1 bar
1. Effective piston area advance stroke
A1 = (50 mm)2 x p/4 = 1963.4 mm2 = 19.63 cm2
2. Effective piston area return stroke
A2 = A1 - (20 mm)2 x p/4 = 1963.4 mm2 - 314.2 mm2 = 1649.2 mm2 = 16.5 cm2
3. Air consumption
Q =
Exercise:
Calculate the air consumption for a DNC-50-100-PPV-A. Piston rod diameter is 25 mm. The number of cycles is 15 per minute.
Theoretical air consumption per 10mm stroke, operating pressure 6bar
Piston [mm] | 32 | 40 | 50 | 63 | 80 | 100 | 125 | 160 | 200 | 250 | 320 |
Piston rod [mm] | 12 | 16 | 20 | 20 | 25 | 25 | 32 | 40) | 40 | 50 | 63 |
Advancing | 0.056 | 0.088 | 0.137 | 0.218 | 0.352 | 0.550 | 0.859 | 1.407 | 2.99 | 3.436 | 5.630 |
Retracting | 0.048 | 0.074 0.080 | 0.115 0.123 | 0.196 0.204 | 0.317 0.330 | 0.515 | 0.803 | 1.319 1.296 | 2.111 2.088 | 3.299 | 5.412 |
Air consumption in normal litres is obtained on the basis of a standard operating pressure pe=6bar. Leakage is therefore not taken into account.
6. Traversal force on piston rod
Traversal forces on the piston rod will cause a surface pressure on the bearing bush of the cylinder. The piston rod acts like a lever. The longer the stroke the higher the surface pressure on the bush. High surface pressure will cause excessive wear of the bush. If the traversal force exceeds the maximum permissible load of the cylinder bush, a external guide or support has to be provided (e.g. Festo FEN guide unit).Example:
A mass of m = 10 Kg has to be moved horizontally for 600 mm by a pneumatic cylinder.
1. What cylinder size has to be selected if there is no external guidance provided?
2. What cylinder/guide unit combination would be capable to do the same job?
7. Allocation of cylinder and valves
The speed of a pneumatic cylinder is dependent on the load, air pressure, length of tubing between cylinder and control valve, diameter of tubing and the flow rate of the control valve. The average speed of a standard cylinder is about 0.1 - 1.5 m/sec. As a guideline for size the following table can be used for sizing the appropriate valve for a certain cylinder diameter. The cylinder speeds which can be achieved in practise, are adequate for most cases.Piston diameter | Valve port size | Nominal width (mm) | Flow rate (l/min) |
to 12 | M3 | 1.5 | 80 |
> 12 - 25 | M5 | 2.5 | to 200 |
> 25 - 50 | G 1/8 | 3.5 | to 500 |
> 50 - 100 | G ¼ | 7.0 | to 1140 |
> 150 - 200 | G ½ | 12.0 | to 3000 |
> 200 - 320 | G ¾, G 1 | 18.7 | to 6000 |
8. Recommendations
The following recommendations are to observed for pneumatic cylinders.Compressed air quality:
Humidity: Pressure dew point up to 10 °C
Temperature: Higher than the dew point of the compressed air, lower than the maximum permitted
ambient temperature.
Solids: Particle size up to 40 mm
Lubrication: Festo pneumatic cylinders have been already given a basic lubrication from the
factory, thus they can be operated with unlubricated as well as lubricated air.
Note: If a cylinder has once been operated with lubricated air, lubrication is always needed, as additional oil flushes out the basic lubrication. |
Up to 1 m/s the factory set lubrication is adequate. From speeds upward 1 m/s lubricated air is recommended for operating cylinders.
Frequency:
If cylinders are operated at the maximum possible speed, pauses between stroke movements have to be arranged. For unlubricated operation, the maximum frequency is to be based on a mean speed of 1 m/s.
Furthermore the limiting values indicated in the catalogue, as regarding to pressures, speeds, masses, moments, lateral forces, buckling loads, actuating forces and temperatures in compliance with technical notes must be adhered to by the user under all circumstances.
If used as recommended, Festo cylinders and combinations of such cylinders are suitable for as good as maintenance-free operations.
5. Pneumatic complete Lecture note
PNEUMATICS
Introduction
Before the 1950's, pneumatics was most commonly used as a working medium in the form of stored energy. During the 1950's the sensing and processing roles developed in parallel with working requirements. This development enabled working operations to be controlled using sensors for the measurement of machine states and conditions. The development of sensors, processors and actuators has led to the introduction of pneumatic systems.
In parallel with the introduction of total systems, the individual elements have further developed with changes in material, manufacturing and design processes.
Pneumatics has for some considerable time been used for carrying out the simplest mechanical tasks, but in more recent times has played a more important role in the sphere of automation.
In the majority of pneumatic applications compressed air is being used for one or more of the following functions :-
to enable sensors to determine status of processes
to allow switching of actuators by using final control elements
to carry out work
Industrial Applications Employing Pneumatics
This is a small selection of applications which have become common place in modern manufacturing processes.
Methods of material handling:-
Clamping
Indexing
Positioning
Orienting
Applications:-
Packaging
Feeding
Metering
Door or chute control
Transfer of materials
Turning and inverting of parts
Sorting of parts
Stacking of components
Stamping and embossing of components
Pneumatic applications can also be used in carrying out machining and working operations. ie:-
Drilling
Turning
Milling
Sawing
Finishing
Forming
Quality control
Why Use Pneumatics?
Pneumatics have distinct advantages and distinguishing characteristics due to the utilisation of compressed air. These can be summarised as below:-
Availability: Air is available practically everywhere in unlimited quantities.
Transport: Air can be easily transported in pipelines, even over large distances.
Storage: A compressor need not be in continuous operation. Compressed air can be stored in a reservoir and removed as required. In addition, the reservoir can be transportable.
Temperature: Compressed air is relatively insensitive to temperature fluctuations. This ensures reliable operation, even under extreme conditions.
Explosion proof: Compressed air offers minimal risk of explosion or fire, hence no expensive protection against explosion is required.
Cleanliness: Unlubricated exhaust air is clean. Any unlubricated air which escapes through leaking pipes or components does not cause contamination. This is an important point when considering the food, wood and textile industries.
Components: The operating components are of simple construction and are therefore relatively inexpensive.
Speed: Compressed air is a very fast working medium. This enables high working speeds to be attained.
Adjustable: With compressed air components, speeds and forces are infinitely variable.
Overload safe: Pneumatic tools and operating components can be loaded to the point of stopping and are therefore overload safe.
In order to accurately define the areas of application of pneumatics, it is also necessary to be acquainted with the negative characteristics:
Preparation: Compressed air requires good preparation or servicing. Dirt and condensate should not be present.
Compressible: It is not always possible to achieve uniform and constant piston speeds with compressed air.
Force: Compressed air is economical only up to a certain force requirement. Under the normal working pressure of 6-7 bar (600 to 700 kPa) and dependent on the travel and speed, the output limit is between 20000 and 30000 Newtons.
Noise level: The exhaust air is loud. This problem has now, however, been largely solved due to the development of sound absorption material and silencers.
Costs: Compressed air is a relatively expensive means of conveying power. The high energy costs are partially compensated by inexpensive components and higher performance.
Factors Involved in System Design and Selection
A comparison with other forms of energy is an essential part of the selection process when considering pneumatics as a control or working medium. This evaluation embraces the total system, from the input signal (sensors) through to the control (processor), to output devices (actuators). Factors to be considered, ie :-
Work or output requirements
Preferred control methods
Resources and expertise available to support the project
Existing systems which are to be integrated with the new project
The above should be analysed and applied to the types of working and control media available, ie :-
Mechanical
Electrical / Electronic
Hydraulic
Pneumatic / Hydro-pneumatic
A combination of the above
A list of selection criteria for the working and control sections of a typical production facility are shown in Table 3.0 below
Table 3.0 Comparison of Working and Control Function Media
WORKING | CONTROL |
Force | Reliability of components |
Stroke | Sensitivity to environmental influences |
Type of motion (linear, rotary) | Ease of maintenance and repair |
Speed | Switching time of components |
Size | Signal speed |
Service life | Space requirements |
Sensitivity | Service life |
Safety and reliability | Training of operators and maintainers |
Energy costs | Modification of the control system |
Controllability | |
Handling | |
Storage |
Overview Of A Pneumatic System
A pneumatic system can be broken down into a number of levels representing hardware and signal flow.
The various levels form a control path for signal flow from the signal (input) to the work (output).
COMPONENTS OF A PNEUMATIC SYSTEM
Energy Supply
The air supply for a particular pneumatic application should be sufficient and of adequate quality.
Air is compressed to approximately 1/7th of its volume by the air compressor and delivered to an air distribution system in the factory. To ensure the quality of the air is acceptable, air service equipment is utilised to prepare the air before being applied to the control system.
Malfunctions can be considerably reduced in the system if the compressed air is correctly prepared. A number of aspects must be considered relative to air preparation :-
Quantity of air required to meet the demands of the system
Type of compressor the be used to produce the quantity required
Storage required
Requirements for air cleanliness
Acceptable humidity levels to reduce corrosion and sticky operation
Low temperature of the air and effects on the system
Pressure requirements
Line sizes and valve sizes to meet demand
Material selection and system requirements for the environment
Drainage points and exhaust outlets in the distribution system
Lubrication requirements, if necessary
Layout of the distribution system to meet demand
As a rule pneumatic components are designed for a maximum operating pressure of 8 - 10 bar (800 - 1000 kPa) but in practice it is recommended to operate at between 5 and 6 bar (500 - 600 kPa) for economic use. Due to the pressure losses in the distribution system the compressor should deliver between 6.5 and 7 bar (650 - 700 kPa) to attain these figures.
An air receiver should be fitted to reduce pressure fluctuations. In normal operation the compressor fills the receiver when required and the receiver is available as a reserve at all times. This reduces the switching cycles of the compressor. See Figure 3.13
If oil is required for the pneumatic system then this should be separately metered using air service equipment. In a normal situation, components should be selected for the control system that does not require lubrication. See Figure 3.14 for an example of an air service unit.
Compressed air filter
Compressed air regulator
Compressed air lubricator
The correct combination, size and type of these elements are determined by the application and the control system demand. An air service unit is fitted at each control system in the network to ensure the quality of air for each individual task.
Compressed air filter:-
The compressed air filter has the job of removing all contaminants from the compressed air flowing through it as well as water which has already condensed. The compressed air enters the filter bowl through guide slots. Liquid particles and larger particles of dirt are separated centrifugally collecting in the lower part of the filter bowl. The collected condensate must be drained before the level exceeds the maximum condensate mark, as it will otherwise be re-entrained in the air stream.
Compressed air regulator :-
The purpose of the regulator is to keep the operating pressure (secondary pressure) virtually constant regardless of fluctuations in the line pressure (primary pressure) and the air consumption.
Compressed air lubricator:-
The purpose of the lubricator is to deliver a metered quantity of oil mist into a leg of the air distribution system when necessary for the use by pneumatic control and working components.
Pneumatic Valves
Pneumatic Valves
Valves can be divided into a number of groups according to their function in relation to signal type, actuation method and construction. The primary function of the valve is to alter, generate or cancel signals for the purpose of sensing, processing and controlling. Additionally the valve can be used as a power valve for the supply of working air to the actuator. Therefore the following categories are relevant :-
Directional control valves
Signalling elements
Processing elements
Power elements
Non-return valves
Flow control valves
Pressure control valves
Combinational valves
Directional Control Valves
Directional control valves in particular, as their name implies, control fluid flow direction. They are applied in pneumatic circuits to provide control functions which:-
control direction of actuator motion (power valve);
select an alternative flow path (shunt valve);
perform logic control functions ("AND", "OR" functions);
stop and start flow of fluid (on - off valve);
sense machine and actuator positions (limit valves).
Directional control valves are classified according to their specific design characteristics:
1. Internal valve mechanism (internal control element) which directs the flow of the fluid. Such a mechanism can either be a poppet disc, a poppet ball, a sliding spool, a rotary plug, or a combination of poppet and spool.
2. Number of switching positions (usually two or three). Some valves may provide more than three, and in exceptional cases up to six switching positions (selector valves).
3. Number of connection ports (not called number of ways!). These ports connect the pneumatic pressure lines to the internal flow channels of the valve mechanism and often also determine the flow rate through it.
4. Method of valve actuation which causes the valve mechanism to move into an alternative switching position and return the valve to its original state.
See circuit presentation for more on valve schematic representation.
Valve Mechanisms
Directional control valves consist of a valve body or valve housing and a valve mechanism. Some valves are mounted to a sub-plate. The ports in the sub-plate or on the valve body are threaded to hold the tube fittings which connect the valve to the fluid conductor lines (tubes). Some valves have the tube fittings moulded into the valve body. This is normally the case where the valve body is made from plastic. The valve mechanism directs the pressurised fluid (compressed air) through the valve body to the selected output ports or stops the fluid from passing through the valve.
Poppet, spool, flat slide, toggle disc and spool/poppet mechanism are predominantly used in directional control valves whereas poppets and balls are the preferred mechanism in check valves and logic "OR" function and "AND" function valves.
Normally Closed And Normally Open Valves
These terms are generally applied to three port valves. The valve shown in Figure 3.15 (top) is a two position three port valve permitting no flow from pressure port 1 to output port 2 in its normal spring biased position. In the case of the normally open valve, Figure 3.15 (bottom), the supply is allowed to stream to output port 2 while the valve is in its normal position. Both valves when operated switch their flow mode to the flow configuration depicted in the left hand square of the valve symbol.

Methods Of Valve Actuation
Methods Of Valve Actuation
The term actuation in relation to pneumatic valves refers to the various methods of moving the valve mechanism into any of its alternative switching positions. Valves can be actuated by five basic methods:
manually
mechanically
electrically
hydraulically
pneumatically
In complex machine applications any of these methods, or combinations of them, may be used to gain optimum control. Manual methods use hand or foot actuators such as levers, push buttons, knobs and foot pedals, electrical methods use A.C. or D.C. solenoids. For pneumatic/electronic control integration some manufacturers make low wattage coils for direct P.L.C. connection. Solenoids range from 12 to 240 volts. Most solenoid and air pilot valves are also equipped with a manual override buttons or plungers. Thus the valve mechanism can be operated even when the air pilot signal or the electrical signal should fail. In hydraulically and pneumatically operated valves the fluid pilot signal is made to act onto a piston or it may act directly onto the valve mechanism and thus move it to its alternative position.
Spring-Actuated Valves
The terms spring-biased or spring-offset, and in the case of three-position valves spring-centred, refer to the application of springs which return the valve mechanism to its rest position as soon as the pilot signal command is cancelled. Such commands, whether they be pneumatic, electric or manual, must be maintained as long as the valve is to remain in its non-normal or actuated position.
A valve without a spring bias is actuated entirely by its external controls, and can therefore "float" or "drift" between its two extreme positions wherever the external control is cancelled. To avoid this, a "detent" mechanism or friction-producing seal rings are used to give the valve a by-stable (or memory) characteristic. Thus when the valve is switched (selected) into a specific flow condition, it will remain in that condition until switched into its alternative condition.
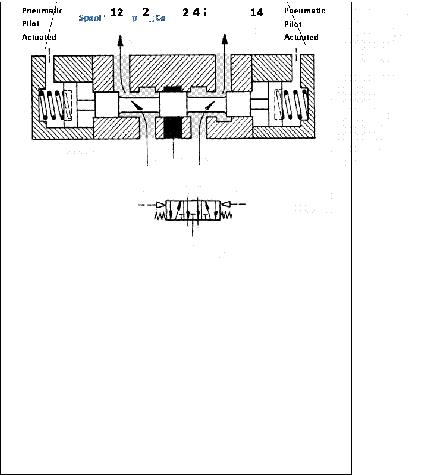

Spool Valves
In modern valve designs, the spool valve, shown in Figure 3.16, is most frequently used. Spool valves offer a number of advantages over poppet and flat-slide valves, see Figure 3.17.
* Spool valves may be used for flow reversal.
* Since flow forces acting onto the lands are equal (equal pressure on equal area) the valve is said to be balanced and uses therefore only small actuating forces.
* Spool valves may operate without elastomeric seals if the spool to body tolerance is kept small (below 0.003 mm) and fluid pressure does not exceed 900 kPa (9 bar).
* Spool valves may be built for more than two switching positions, but then the spool is normally spring centred, see Figure 3.16, or hand lever operated with detented positions.
With spool valves care must be taken to mount the valve onto a reasonably flat (preferably machined) surface, since only slight body distortion may warp the valve body sufficiently to make the closely toleranced and lapped spool seize, or hinder it from moving freely when actuated. The same may also be said for bolting the valve tool firmly against its mounting surface.
Spool valves are susceptible to contamination from poorly conditioned compressed air. Therefore close monitoring of the air quality - its filtration and lubrication is required
Flat Slide Valves
Flat slide valves are a modern adaptation of the old steam valve used on steam locomotives. The flat slide is carried to and fro by a grooved piston. See Figure 3.17. The piston may either be air-pilot signal or spring or solenoid/air pilot operated. The valve cannot be flow reversed (port 1 cannot be used as port 3 and vice versa) but it offers the advantage of a combined exhaust port which may be useful for actuator speed control. Since compressed air forces the flat slide against its bearing surface, the flat slide provides absolute leak free (pressure assisted) sealing and automatically adjusts for wear on its gliding surface. Flat slide valves are also made with a double slide to gain two exhaust ports and some valves have also snap action toggle discs instead of carrier spools.
Poppet Valves
Poppet valves offer at least two significant advantages over spool and flat slide valves.
* Poppet valves are robust and do not require lubrication. They have no close tolerance gaps on moving parts since they provide head-on instead of dynamic sealing.
* Poppet valves provide positive and air pressure assisted sealing (air pressure acts onto the underside of the poppet, See Figure 3.18
Due to the sealing design, poppet valves require a much higher operating force than any other valve design type and thus are often built with air-pilot operating assistance. The operating mechanism (roller, plunger, lever) opens a small pilot valve. This pilot valve directs pilot air to a large piston or diaphragm which operates the poppet mechanism.
True poppet valves are not flow reversible (port 1 cannot be interchanged for port 3). Hence some component manufacturers offer a poppet valve for normally open as well as for normally closed flow configuration.
Friction Free Valves (Toggle Disc Valves)
These valves are specifically designed to combine all the advantages of spool and poppet valves and at the same time eliminate all the disadvantages of spool and poppet valves. Friction free valves, as their name implies, work totally friction free and offer also the following advantages :- See Figure 3.19.
* High air flow characteristics. Equal or better than spool valves.
* Static, long life sealing. The seal ring moves head-on against the sealing lips (same as in poppet valves).
* The seal carrier (spool) is suspended between the two pre-tensioned discs and moves friction-free to and fro.
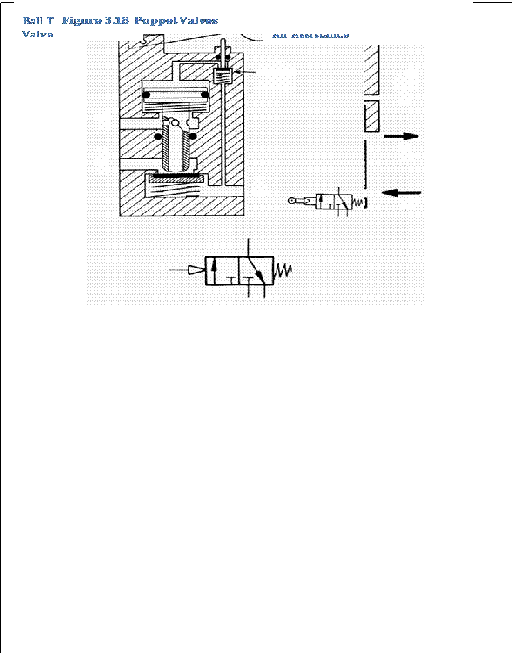
* Actuation of the disc moves it over the toggle point and tension forces snap the disc rapidly into its alternate position, thus giving rapid flow switching and memory function.
* Air contamination cannot impair valve movement and lubrication of the compressed air is not required.
* The valve is flow reversible which means port 1 may become port 3 and vice versa.
As a power element the directional control valve must deliver the required quantity or air to match the actuator requirements and hence there is a need for larger volume flow rates and therefore larger sizes. This may result in a larger supply port or manifold being used to deliver the air to the actuator.
Flow Control For Pneumatics
The flow control valve restricts or throttles the air in a particular direction to reduce the flow rate of the air and hence control the signal flow. If the flow control valve is left wide open then the flow should be almost the same as if the restrictor is not fitted. In some cases it is possible to infinitely vary the restrictor from fully open to completely closed. If the flow control valve is fitted with a non-return valve then the function of flow-control is unidirectional with full free flow in one direction. A two way restrictor restricts the air in both directions of flow and is not fitted with the non-return valve. The flow control valve should be fitted as close to the working element as is possible and must be adjusted to match the requirements of the application.
Flow control valves are frequently used in pneumatic systems. Their use is limited to the control of compressed air to and from the actuator and their main functions are :-
* to control the maximum speed of the actuator piston and its attached
load,
* to provide constant speed for the main part of the actuator piston stroke when acceleration is completed,
* to cushion the load impact at the end of the actuator stroke or decelerate a load to a lower speed,
* to prevent free falling of a heavy load on vertical movements.
Simple Restrictor Type Flow Control
This valve, being variable as far as the cross section of the orifice is concerned, is therefore also called a variable restrictor flow control valve or variable orifice flow control valve. It is mostly used on the outlet of the power valves and restricts the flow of air in both directions See Figure 3.2
Theses valves consist of a valve body and a throttling screw which adjusts the orifice cross-section to achieve the desired speed on the actuator.
Variable Restrictor With Free Reverse Flow
Where speed control (flow control) in only one valve direction is required, a check valve is built into the flow control. This permits unrestricted flow of air in the reverse direction. See Figure 3.21
The construction of this type of valve apart from the inbuilt check valve is identical to the simple restrictor type. The check valve consists of a rubber ring, which can flex upward if reverse flow is required, and a ring hub to hold the disc onto the check valve orifice during the throttling function.
Some pneumatic component manufacturers also make miniature type flow control valves which are directly built into the exhaust ports of the power valve. Others manufacture an actuator swivel-fitting which contains a small flow control valve with free reverse flow. Such inbuilt valves save space, extra connectors and installation costs.
Hydraulic Check Speed Control
Any form of pneumatic speed control no matter how effective , can never provide absolute speed consistency. See Figure 3.22. Speed consistency is imperative for machining operations or applications in manufacturing where the quality of the product depends on absolute uniform speed over the entire stroke length.
For such cases an hydraulic check cylinder may be used. The hydraulic oil, which is virtually incompressible, is used to provide precise and uniform speed control which is independent and unaffected by load variations of the pneumatic actuator. The pneumatic actuator is linked to the hydraulic check
cylinder. The force needed to move the hydraulic piston and its piston rod comes from the pneumatic actuator which literally drags the hydraulic piston along. The displaced oil is forced via a hydraulic flow control valve which provides the required speed control. An oil reservoir with a spring loaded piston compensates for the differing oil volumes displaced by the hydraulic piston and makes up for oil losses due to piston rod lubrication.
Installation Methods For Restrictor Type Flow Controls
Two basic methods are commonly used to install restrictor type flow controls. These methods are widely known as meter-in flow control and meter-out flow control. Both methods have their distinct advantages and disadvantages, but where possible meter-out should be given preference.
Meter-in speed control
Where an actuator has insufficient air volume on the exhaust side of the moving piston, so that the exhausting air cannot be sufficiently compressed by the flow control to cause an air-cushion, then meter-in speed control must be used. This is mainly the case with small diameter or short stroke actuators. Meter-in must also be used for single acting actuators.
Meter-out speed control
Meter-out provides the necessary back-pressure which is imperative for smooth and constant piston speed.
The back pressure brought about by meter-out speed control reduces the force output of the actuator, which demands that a larger piston must be selected to move the given load. The advantages gained from meter-out speed control are numerous and may be listed as :-
* A free falling. suspended or supported load can be controlled.
* The back pressure caused by a meter-out speed control resists the advancing piston which is driven forward by the pressure on the opposite side. This form of speed control provides excellent and constant control of the actuator speed.
* Pneumatic end-cushioning is greatly enhanced with the air pressure cushion caused by the meter-out speed control restrictor valve.
Power valve exhaust port speed control
To achieve optimal speed control it is advisable to mount the flow restrictors (speed control valves) directly onto the actuator.
Frequently these valves are mounted onto the exhaust ports of the power valves. With this installation, however, there is risk of damaging the pneumatic seals inside the power valve or rupturing the air hose between the actuator and the power valve. This may occur because of pressure intensification induced by an oversize piston rod.
Non Return Valves And Derivatives
The non-return valve allows a signal to flow through the device in one direction and in the other direction blocks the flow. There are many variations in construction and size derived from the basic non-return valve. Other derived valves utilise features of the non-return valve by the incorporation of non-return elements. The non-return valve can be found as an element of the one way flow control valve, quick exhaust valve, shuttle valve and the two-pressure valve.
"AND" Function Valve (two pressure valve)
Some component manufacturers make a special purpose "AND" function valve (two pressure valve). This valve ensures that both expected input signals must be present on the valve before either of them is permitted to pass through to the outlet port. The first arriving signal shifts the valve element (twin poppet), and the weaker or second arriving signal finds its way to the outlet port; thus it may be said that both input signals are required. The valve is extremely simple in its construction and costs less than an air pilot operated spool or spool/poppet valve. This type of valve is widely available and has the advantage that the weaker signal may be used as the pilot signal and the stronger signal passes through the valve. See Figure 3.23
"OR" Function Valve (shuttle valve)
Most component manufacturers make a special purpose "OR" function valve (shuttle valve). See Figure 3.24 This valve connects either input 1 or input 2 to the outlet port A, but prevents any cross flow from input 1 to input 2 or vice versa. It is to be noted that a T-connector must not be used to merge two pilot signal lines.
The pneumatic cylinder has a significant role as linear drive unit, due to its relatively low cost, ease of installation, simple and robust construction and availability in various sizes and stroke lengths.
The pneumatic cylinder has the following general characteristics:
For example:-
Diameters 6 to 320 mm
Stroke lengths 1 to 2000 mm
Available forces 2 to 50000 N
Piston speed 0.02 to 1 m/s
Pneumatic linear actuators are used to convert the stored (static) energy of compressed air into linear mechanical force or motion. Although the actuator itself produces linear motion, a variety of mechanical linkages and devices may be attached to it to produce a final output force which is rotary, semi-rotary or a combination of linear and rotary. Levers and linkages may also be attached to achieve force multiplication or force reduction as well as an increase or reduction of motion speed. Actuators can be broken down into groups:
Linear actuators
Single acting cylinder
Double acting cylinder
Rotary actuators
Vane type
Air motors
The generation of linear thrust force with a pneumatic actuator is very simple and direct. The compressed air when delivered to one end of the actuator, acts against the piston area and produces a force against the piston (force = pressure x area). The piston with the attached piston rod starts to move in linear direction as long as the reacting force is smaller. The developed force is used to move a load which may be attached either to the protruding piston rod or to the actuator housing. The distance through which the piston travels is known as the stroke.
Single acting actuators
Single acting actuators produce pneumatic force in one direction only. These actuators may be mounted in vertical direction, thus permitting the previously moved or lifted load to return the piston to its initial position. When the actuator must be mounted horizontally or when no external force can be used to return the piston, then an inbuilt spring is used to cause retraction or return of the piston.
When using a single acting actuator the force available from the air operated stroke is reduced by the opposing spring force. It must be noted that the force due to the spring compression is progressively decreasing along its stroke. Single acting actuators are usually built with a stroke length up to 100 mm.
Some manufacturers of pneumatic actuators make a special type of single acting actuator, called a short stroke clamping cylinder or diaphragm actuator. These actuators have extremely short strokes ranging from 1 to 10 mm and piston areas ranging from 100 to 3000 mm2, whereby the large piston (diaphragm) actuators normally have the extremely short strokes of 1 to 2 mm.
Such clamping actuators are normally retracted by either an inbuilt spring or by the pre-tensioned diaphragm.
Double acting actuators
Double acting actuators permit the application of pneumatic force in both stroke directions. However, the retraction stroke develops a much smaller force than the extension stroke, since the compressed air acts on a smaller area known as the annular area. See Figure 3.25
Double-ended actuators with rods protruding on both actuator ends are used where the developed force must be equal for both piston-rod movement directions (extension and retraction). Since the volumes to be filled with compressed air are equal for extension and retraction, the resulting piston speeds are also equal for both strokes. Double ended actuators provide also better piston rod guidance since loads are borne over two bearing bushes; one on each actuator end. Double ended actuators may also prove advantageous where the limit valves (position sequence valves) or electrical limit switches cannot be placed near the reciprocating piston rod. This may be the case where the transported load moves in a hostile environment, or in an area of extreme heat, or in a liquid. In such a case, the rear piston rod is used to actuate the limit valves and the front piston rod moves the load.
Pneumatic end-position cushioning (simply called cushioning) refers to the controlled deceleration of the mass in motion during its final part of the actuator stroke. The kinetic energy released on impact at the stroke end must be absorbed by the internal stroke limit stops. These stops are usually a protruding bush which is an extended part of the end caps.
For large and fast moving masses or for actuators with piston diameters above 25 mm pneumatic end-cushioning is recommended. Figure 3.26 shows a cross-section of a pneumatic cushioning mechanism built into the end caps of pneumatic actuators. The piston is fitted with a tapered cushioning bush (boss). When this bush enters into the air exit bore of the end cap (during the final part of the stroke), the main air exit begins to shut until it finally closes off completely. This first stage of exit flow throttling may cause an initial slight speed reduction. The remaining air in the annular cavity around the cushioning boss is now trapped and the momentum of the mass carries the piston on against the trapped air; thus compressing it to a high pressure. As the pressure rises, the resulting resisting force forms a cushion and begins to decelerate the piston and its mass (load)
As the kinetic energy is dispelled, the mass is slowed down to a much reduced speed which matches the rate of air flow permitted and adjusted by the cushioning valve. A check valve is also built in as part of the cushioning mechanism. This check valve allows full air flow in reverse direction to achieve fast and full force break-away from the end position.
Actuator failure
Standard type actuators are not designed to absorb piston rod side loading. Thus actuators must be mounted with care and accuracy, to ensure that the load moves precisely parallel and in alignment with the actuator centre line.
For many applications the piston rod is best fitted with a clevis or a spherical bearing rod-eye or the actuator must be allowed to swivel around a trunion mount, permitting it to swing as the direction of the load changes. A self aligning piston-rod coupling can also be used to compensate for both angular and radial misalignment, but the angular misalignment must not exceed 4 degrees in either direction and the radial alignment must not be more than 1 mm.
Failure of the rod bearing usually occurs when side load is not detected early enough or cannot be avoided. In such cases one may use a double ended piston rod type actuator or an actuator with oversize piston rod which is less flexible than a standard size piston rod.

Rodless actuators
Rodless actuators
Few pneumatic devices have enjoyed such immediate success and widespread application as the rodless actuator. An ingenious design eliminates the piston rod and cuts installation length almost to half compared to conventional double acting linear actuators. Presently, there are four design types of rodless actuators available.
Probably the most popular of these is the "Origa Rodless Cylinder". With the "ORIGA" rodless actuator principle, force from the moving piston is transferred to the carriage by means of a piston yoke that slides along the barrel slot. Its slot seal, also claiming to be absolutely free of air leaks, consists of a thin steel strip on the inside of the tube and a dust or dirt seal strip on the outside of the tube. Both steel strips pass through the piston yoke, which separates them as the piston slides along, and closes them again and forces them against a holding magnet attached to the barrel slot. The air inlet holes are located in the end-caps and so are the end-cushioning bushes. The "ORIGA" rodless actuator is extremely rigid due to its extruded type barrel construction and provides a maximum force output of 2600 newtons with a piston diameter of 80 mm at a maximum air pressure of 800 kPa (8 bar). "ORIGA" actuators are made with 80, 63 and 40 mm piston diameter and a maximum travel distance of 7000 mm See Figure 3.28.
Air Motors (Rotary Actuators)
By the use of rack and pinion drives or other mechanical systems the linear actuator (or cylinder) can be used to provide a rotary movement and so provide a torque output. Although such swivel actuators are suitable for many applications, they are not to be mistaken for air motors. Swivel actuators or semi-rotary actuators are generally built and designed to provide a rotary torque output up to a 360 degree rotation.
Air motors, however, produce a continuous torque output - thus driving a revolving drive shaft - and are regarded as the pneumatic counterpart to an electric motor. Revolving air motors are put to extremely diverse uses: from dentist's drill to the drive for a caterpillar tracked tunnel boring machine. The manufacturing industry in particular is a large user of a wide range of types and sizes of air motor driven tools such as nut runners, drills, screw drivers, grinders and sanders.
Air motors use the characteristics of compressed air power transmission to their best advantage, which means they are easily adjusted for varying speeds and torque, can be reversed, can safely be operated in an explosive environment, and can be stalled indefinitely (thus are overload safe). These
operational characteristics, combined with their excellent power features, that make air motors so versatile and widely accepted.
Air motors can be classified into five basic types, each of which produces a specific range of power output and has an operating characteristic which makes it ideally suited for a particular industrial application. These types are :-
vane motors
gear motors
piston motors
turbine motors
roots motors
In each design type the pressure exposed driving surface area must be connected mechanically to the motor output shaft. Inlet and outlet air must have a timed porting arrangement to produce continuous rotation (this feature does not apply to turbine motors).
Maximum performance varies greatly between the various design types of air motors and is determined by :-
* the ability of its internal pressure exposed areas to withstand the forces acting upon them;
* the internal leakage characteristics of the moving parts which seal the high pressure inlet from the low pressure outlet
* the efficiency of the mechanisms which link the moving pressure exposed parts to the motor drive shaft (output shaft).
Vane motors
The vane motor is the most common type of air motor used in the manufacturing industry. It covers a large range of power outputs from less than 1 kW to around 25 kW, which makes them versatile and widely accepted. See Figure 3.29 shows a cross section of a reversible vane motor. A rotor shaft which carries a number of sliding vanes is mounted eccentrically in a cylindrical casing or stator. The vanes are usually made of fibre which has excellent wear properties, and the more vanes used (up to a practical limit) the better the starting torque will be. However, increased friction from the vanes reduces efficiency.
In vane motors torque is produced by the compressed air acting onto the pressure exposed rectangular area of the vanes. These vanes in fact seal the low pressure exhaust port from the high pressure inlet port. According to Pascal's Law, which also applies to pneumatic systems, pressure acts undiminished in all directions and acts also with equal force on equal areas. It is therefore obvious that the motor shown must turn in a clockwise direction, since the sum of all vane areas being pressurised in a clockwise direction is much larger than the sum of vane areas being pressurised in an anticlockwise direction. As the rotor continues to rotate in this manner, any residual air remaining between the blades is vented via the anticlockwise supply port B. If the motor is to be operated to produce torque in the opposite direction, the anticlockwise port B is pressurised and port A is vented. The action is then exactly the reverse of that described for clockwise rotation.
As the motor turns the sliding vanes follow the contour of the cam ring (housing), thus forming sealed cavities. Since the vanes must seal and thus maintain cam ring contact at all times, and centrifugal force is absent during motor start, these vanes are usually spring loaded or air pressure loaded for smaller motors. See Figure 3.3
During motor rotation the compressed air in the pockets between the vanes is permitted to expand, since the pockets also expand as they rotate towards the exhaust opening. This permits the potential energy stored in the compressed air to be used and thus the "technical work" of the motor is increased and its efficiency is therefore also increased.
Figure 3.1 Hardware and Signal Flow
The elements in the system are represented by symbols which indicate the function of the element. The symbols can be combined to represent a solution for a particular control task using a circuit diagram. The circuit is drawn with the same structure as the signal flow diagram above. A breakdown of these primary levels can be seen in Figure 3.11.
Figure 3.11 Primary Levels of a Pneumatic System
The directional control valve (DCV) may have a sensing, a processing or an actuating control function. If the DCV is used to control a cylinder motion, then it is a control element for the actuator group. If it is used in the function of processing signals, then it is defined as a processor element. If it is used to sense motions, then it is defined as a sensor. The distinguishing feature between each of these roles is normally the method of operating the valve and where the valve is situated in the circuit diagram. This can be seen in Figure 3.12.
SYMBOLS AND STANDARDS IN PNEUMATICS
Symbols and descriptions of components
The development of pneumatic systems is assisted by a uniform approach to the representation of the elements and the circuits. The symbols used for the individual elements must display the following characteristics:
Function
Actuation and return actuation methods
Number of connections (all labelled for identification)
Number of switching positions
General operating principle
Simplified representation of the flow path
A symbol does not represent the following characteristics:
Size or dimensions of the component
Particular manufacturer, methods of construction or costs
Orientation of the ports
Any physical details of the element
Any unions or connections other than junctions
The symbols for the energy supply system can be represented as individual elements or as combined elements. The choice between using simplified or detailed symbols is dependent upon the purpose of the circuit and its complexity. In general where specific technical details are to be given such as requirements for non-lubricated air or micro-filtering, then the complete detailed symbol should be used. If a standard and common air supply is used for all components, then the simplified symbols can be used. For trouble-shooting the detailed symbols are more suitable. But the detail should not add to the complexity of the circuit for reading.
Directional control valves
The directional control valve is represented by the number of controlled connections and the number of positions. Each position is shown as a separate square. The designation of the ports is important when interpreting the circuit symbols and the valve as fitted to the physical system. To ensure that the correct lines, connections and valves are physically in place, there must be a relationship between the circuit and the components used.
Therefore all symbols on the circuit must be designated and the components used should be labelled with the correct symbol and designations. See Figure 3.32
A numbering system is used to designate directional control valves and is in accordance with ISO 5599 See Figure 3.33
Port or Connection ISO 5599
Pressure port 1
Exhaust port 3
Exhaust ports 5, 3
Signal outputs 2, 4
Pilot line opens flow 1 to 2 12
Pilot line opens flow 1 to 4 14
Pilot line flow closed 10
Methods of actuation
The methods of actuation of pneumatic directional control valves is dependent upon the requirements of the task. When applied to a directional control valve, consideration must be given to the method of initial actuation of the valve and also the method of return actuation. Normally these are two separate methods. They are both shown on the symbol either side of the position boxes. There may also be additional methods of actuation such as manual overrides, which are separately indicated.
Pressure regulating valves
Pressure regulating valves are generally adjustable against spring compression. The symbols are distinguished according to the following types:
Pressure sensing: downstream, upstream or external
Relieving or non-relieving and fluctuating pressure
Adjustable or fixed settings
The symbols represent the pressure valve as a single position valve with a flow path that is either open or closed initially. In the case of the pressure regulator the flow is always open, whereas the pressure sequence valve is closed until the pressure reaches the limit value as set on the adjustable spring. See figure 3.34
Non-return valves and derivatives
The non-return valve (check valve) is the basis for the development of many combined components. There are two main configurations for non-return valves, with and without the spring return. See figure 3.35
Flow control valves
Most flow control valves are adjustable. The one way flow control valve permits flow adjustment in one direction only with the non-return fitted. The arrow shows that the component is adjustable but does not refer to the direction of flow; it is diagrammatic only. See figure 3.35
Linear actuators
The linear actuators or cylinders are described by their type of construction and method of operation. The single acting cylinder and the double acting cylinder form the basis for design variations. The use of cushioning to reduce loads on the end caps and mountings during deceleration of the piston is important for long-life and smooth operation. The cushioning can be either fixed or adjustable. The cushioning piston is shown on the exhaust air side of the piston. The arrow indicates adjustable cushioning and not the direction of cushioned motion. See figure 3.35
Rotary actuators
Rotary actuators are divided into continuous motion and limited angle of rotation. The air motor is normally a high speed device with either fixed or adjustable speed control.
Units with limited angle of rotation are fixed or adjustable in angular displacement. The rotary actuator may be cushioned depending upon the load and speed of operation. See figure 3.36
Auxiliary symbols
There are a number of important symbols for accessories which are utilised in conjunction with pneumatics. These include the exhaust air symbols, visual indicators and the methods of connection of components. See figure 3.36
Safety requirements for pneumatic systems
There are a limited number of standards and regulations for pneumatic systems. Therefore for all factors affecting safety, reference must be made to existing general guidelines and regulations from a number of different engineering fields.
Consideration should be given to the following guidelines when operating pneumatic cylinders under clamping conditions.
The control system for the pneumatic clamping devices should be designed or arranged in such a way as to avoid accidental operation. This can be achieved by means of:
Manually-operated switching devices with protective covers
Control interlocks
Two handed operation
Precautions must be taken to prevent hand injuries caused by the clamping device. Machines with pneumatic clamping devices must be equipped in such a way that the drive of the working spindle or feed cannot be switched on until the clamping is confirmed complete. This can be achieved by checking the clamping conditions by means of:
Pressure transducers, or
Pressure sequence valves
A failure of the air supply must not cause the clamping device to open during the machining of a clamped workpiece. This can be achieved by means of:
Pressure reservoirs
Control interlocks (memory valves)
Environmental pollution
Two forms of environmental pollution may occur in pneumatic systems:
Noise: caused by the escape of compressed air
Oil mist: caused by lubricants which have been introduced at the compressor via a service unit and which are discharged into the atmosphere during the exhaust cycles.
Exhaust noise
Measures must be taken against excessive exhaust noise. This can be achieved by means of:
Exhaust silencers
Silencers are used to reduce the noise at the exhaust ports of valves. They operate on the principle of exhaust air flow control by creating a greater or lesser flow resistance. Normal silencers have only limited influence on the speed of the piston rod. In the case of throttle silencers, however, the flow resistance is adjustable. These silencers are used to control the speed of the cylinder piston rod and the valve response times. Another method of noise reduction is to fit manifolds with connections to the exhaust ports of the power valves and thus to discharge the air via a large common silencer or to return it to a reservoir.
Oil mist
The exhaust air of mechanically driven tools or mechanically controlled machines contains atomised oil which often remains in a room for some considerable time in the form of a vapour, which can be breathed in. Pollution of the environment is particularly acute in cases where a large number of air motors or large-diameter cylinders are fitted in an installation. Effective countermeasures must be taken to reduce the amount of oil mist that escapes to the atmosphere.
Operational safety
When maintaining or working with pneumatic systems, care must be taken in the removal and the reconnection of air lines. The energy stored in the tube or pipe will be expelled in a very short time with enough force to cause severe whiplash of the line which can endanger personnel. Where possible the air should be isolated at two different points, removing the air pressure before the disconnection is made. An additional danger is in the disturbance of particles due to the air blast which causes eye hazards.
CIRCUIT PRESENTATION AND CONTROL PROBLEM ANALYSIS
Recommendations for circuit array
There are no international standards for circuit presentation and layout at present, so some well proven principles are listed below:
Draw all symbols where possible in horizontal position and attach lines to the right hand square for two position valves or the centre square for three position valves
Do not mirror-invert symbols if avoidable, since this practice confuses the comprehension of signal direction, fluid-flow and valve function
Draw all valves in their de-actuated, unpressurised rest position, except for those valves which are actuated either by a lever, cam or machine part, when the machine is at rest, or at the end of a cycle. For such valves one must indicate with a cam or similar device that the valve is actuated and all attachment and pressure lines are to be connected to the left hand square.
Two-position valves which are not spring biased and can freely assume both switching positions (bi-stable valves, memory valves or detented valves) may be drawn in whatever flow-path configuration is demanded by the actuator position or initial position when the machine is at rest. But here again, the pressure lines should be connected to the right hand square for memory valves in sequential control circuits which maintain their last selected position to provide the start signal for a new machine cycle.
Where complex schematic drawings are being generated and position sensing valve signals or pressure sensing valve signals have to be distributed to a number of destinations for circuit interlocking, it is advisable to adopt the "bus-bar" distribution system, see Figure 3.38. The bus-bar should be regarded as a manifold line with both extremities closed off.
Control Problem analysis
The first step is the definition of objectives for the project with a clear definition of the problem(s). Design or development of the solution is not

involved at the analysis stage. A flow chart of the total project plan can be developed to define the step-orientated processes.
involved at the analysis stage. A flow chart of the total project plan can be developed to define the step-orientated processes.
The grouping of the total control circuit into sub-circuits seems to be one of the main difficulties which confront circuit designers. However, these obstacles can be drastically reduced by analysing the total control problem and then splitting the design into four main categories:
power circuit
sequential circuit
fringe condition modules
combinational circuit
The power circuit consists of the actuators and their directional control valves (power valves). It also includes the speed control valves and compressed air lines which connect the actuators to the power valves.
That part of the circuit which controls the stepping or sequencing of the actuators is generally called the sequential circuit. It consists of memory valves, "AND" function, "OR" function and time-delay valves.
The fringe condition circuits, which preferably are arranged in modules, affect the sequential circuit at its fringe and generally affect its start or stop characteristics (start permitted or not, emergency stop, etc.). These fringe condition modules are added in the final part of circuit deign and are designed separately.
There are two primary methods for constructing circuit diagrams:
The so-called intuitive methods, also frequently termed conventional or trial-and-error methods
The methodical design of a circuit diagram in accordance with prescribed rules and instructions
Whereas much experience and intuition is required in the first case and above all, a great deal of time where complicated circuits are concerned; designing circuit diagrams of the second category requires methodical working and a certain amount of basic theoretical knowledge.
Regardless of which method is used in developing the circuit diagram, the aim is to end up with a properly functioning and reliable operating control. Importance is now attached to operational reliability and ease of maintenance by a clear layout and documentation. Regardless of which method and which technique is used to produce a circuit diagram, fundamental knowledge of the devices concerned and a knowledge of the switching characteristics of these devices, is required
6.Pneumatic tutorial problems
SIMPLE PNEUMATIC CIRCUIT EXERCISES
Direct control of a pneumatic cylinder
The simplest level of control for the single or double acting cylinder involves direct control signals. Direct control is used where the flow rate required to operate the cylinder is relatively small, and the size of the control valve is also small with low actuating forces. If the valve is too large, the operating forces required may be too great for direct manual operation.
Exercise 1: Direct control of a single acting cylinder
The Problem
A single acting cylinder of 25mm diameter is to clamp a component when a push-button is pressed. As long as the push-button is activated, the cylinder is to remain in the clamped position. If the push-button is released, the clamp is to retract.
Exercise
a) Draw the circuit diagram for the problem.
b) Designate the valves and indicate the numbering system for the connections (ports).
c) Describe the operation of the circuit.
FIG. Exercise 1
Exercise 2: Direct control of a double acting cylinder
The Problem
A double acting cylinder is to extend when a push-button is operated. Upon release of the push-button the cylinder is to retract. The cylinder is of small bore (25mm diameter) requiring a small flow rate to operate at the correct speed.
FIG. Exercise 2
Exercise
a) Draw the circuit diagram for the problem.
b) Designate the valves and indicate the numbering system for the connections (ports).
Exercise 3 : Indirect control of a single acting cylinder
The Problem
A large diameter single acting cylinder is to extend upon operation of a push-button valve. The push-button valve is situated at a remote position. Therefore indirect control should be used to operate the cylinder. The cylinder is to retract once the remote push-button is released.
FIG. Exercise 3
Exercise
a) Draw the circuit diagram for the problem.
b) Designate the valves and indicate the numbering system for the connections (ports).
c) Describe the operation of the circuit.
d) Explain why the remote positioning of a valve is advantageous
Exercise 4: Indirect control of a double acting cylinder
The Problem
A double acting cylinder is to extend when a push-button is operated. Upon release of the push-button the cylinder is to retract. The cylinder is 250mm diameter and consumes a large volume of air.
FIG. Exercise 4
Exercise
a) Draw the circuit diagram for the problem.
b) Designate the valves and indicated the numbering system for the connections.
c) Describe the operation of the circuit.
Exercise 5: The logic AND function; the two pressure valve
The Problem
A transfer station removes a product from a conveyor belt. If the product is detected as present and if the operator presses the push-button, the pick-up cylinder 1.0 extends. The product is sensed by a 3/2 way roller lever valve. Upon the release of the push-button the cylinder 1.0 is to retract to the initial position.
FIG. Exercise 5
Exercise
a) Draw the circuit diagram for the problem.
b) Designate the valves and indicated the numbering system for the connections.
c) Describe the operation of the circuit.
Exercise 6: The logic OR function; the shuttle valve
The Problem
A cylinder is used to transfer parts from a magazine. If either a push button or a foot pedal is operated, then the cylinder is to be extended. Once the cylinder is fully extended, it is to retract to the original position. A 3/2 way roller lever valve is to be used to detect the full extension of the cylinder.
FIG. Exercise 6
Exercise
a) Draw the circuit diagram for the problem.
b) Designate the valves and indicated the numbering system for the connections.
c) Describe the operation of the circuit.
Exercise 7: Memory circuit and speed control of a cylinder
The Problem
A double acting cylinder pushes products from a magazine onto a chute. The cylinder is to extend fully when a push-button is operated. The cylinder is not to retract until full extension is reached. Extension is confirmed by a roller lever valve. The cylinder is to continue forward even if the push-button is released before full extension is reached. The speed of the cylinder is to be adjustable in both directions
of motion.
FIG. Exercise 7
Exercise
a) Draw the circuit diagram for the problem.
b) Designate the valves and indicated the numbering system for the connections.
Questions
1. What is the switching status of the memory valve when first fitted to the system and therefore what position will the cylinder be in?
2. Describe the operation of the circuit.
3. If the push-button is held operated even after full extension is reached, what effect will this have on the cylinder retraction?
4. What is the effect on the operation of fitting the roller lever valve at the mid-stroke position of the cylinder, i.e. not at the full extension position?
Exercise 8: The time delay valve
The Problem
A double acting cylinder is used to press together glued components. Upon operation of a push-button, the clamping cylinder extends and trips a roller lever valve. Once the fully extended position is reached, the cylinder is to remain for a time of T=6 seconds and then immediately retract to the initial position. A new start cycle is only possible after the cylinder has fully retracted. The cylinder extension is to be slow and the retraction adjustable but relatively fast.
FIG. Exercise 8
Exercise
a) Draw the circuit diagram for the problem.
b) Designate the valves and indicated the numbering system for the connections.
c) Describe the operation of the circuit.
SIMPLE PNEUMATIC CIRCUIT EXERCISES
Direct control of a pneumatic cylinder
The simplest level of control for the single or double acting cylinder involves direct control signals. Direct control is used where the flow rate required to operate the cylinder is relatively small, and the size of the control valve is also small with low actuating forces. If the valve is too large, the operating forces required may be too great for direct manual operation.
Exercise 1: Direct control of a single acting cylinder
The Problem
A single acting cylinder of 25mm diameter is to clamp a component when a push-button is pressed. As long as the push-button is activated, the cylinder is to remain in the clamped position. If the push-button is released, the clamp is to retract.
Exercise
a) Draw the circuit diagram for the problem.
b) Designate the valves and indicate the numbering system for the connections (ports).
c) Describe the operation of the circuit.
FIG. Exercise 1
Exercise 2: Direct control of a double acting cylinder
The Problem
A double acting cylinder is to extend when a push-button is operated. Upon release of the push-button the cylinder is to retract. The cylinder is of small bore (25mm diameter) requiring a small flow rate to operate at the correct speed.
FIG. Exercise 2
Exercise
a) Draw the circuit diagram for the problem.
b) Designate the valves and indicate the numbering system for the connections (ports).
Exercise 3 : Indirect control of a single acting cylinder
The Problem
A large diameter single acting cylinder is to extend upon operation of a push-button valve. The push-button valve is situated at a remote position. Therefore indirect control should be used to operate the cylinder. The cylinder is to retract once the remote push-button is released.
FIG. Exercise 3
Exercise
a) Draw the circuit diagram for the problem.
b) Designate the valves and indicate the numbering system for the connections (ports).
c) Describe the operation of the circuit.
d) Explain why the remote positioning of a valve is advantageous
Exercise 4: Indirect control of a double acting cylinder
The Problem
A double acting cylinder is to extend when a push-button is operated. Upon release of the push-button the cylinder is to retract. The cylinder is 250mm diameter and consumes a large volume of air.
FIG. Exercise 4
Exercise
a) Draw the circuit diagram for the problem.
b) Designate the valves and indicated the numbering system for the connections.
c) Describe the operation of the circuit.
Exercise 5: The logic AND function; the two pressure valve
The Problem
A transfer station removes a product from a conveyor belt. If the product is detected as present and if the operator presses the push-button, the pick-up cylinder 1.0 extends. The product is sensed by a 3/2 way roller lever valve. Upon the release of the push-button the cylinder 1.0 is to retract to the initial position.
FIG. Exercise 5
Exercise
a) Draw the circuit diagram for the problem.
b) Designate the valves and indicated the numbering system for the connections.
c) Describe the operation of the circuit.
Exercise 6: The logic OR function; the shuttle valve
The Problem
A cylinder is used to transfer parts from a magazine. If either a push button or a foot pedal is operated, then the cylinder is to be extended. Once the cylinder is fully extended, it is to retract to the original position. A 3/2 way roller lever valve is to be used to detect the full extension of the cylinder.
![clip_image009[1] clip_image009[1]](https://blogger.googleusercontent.com/img/b/R29vZ2xl/AVvXsEiH5kGUwPRVVjR63wdrATuOYIg4BuIx2BNi8bDpJviz2033b2WdKeY-loAejPihNfXD07Nhy-uUa_KWm9F_0RZ33Bokb7EAAKE4ctNT2aegiCWHp3Y4Ckp2CX6TQUUTa9ZP7U9VybyhyY0/?imgmax=800)
FIG. Exercise 6
Exercise
a) Draw the circuit diagram for the problem.
b) Designate the valves and indicated the numbering system for the connections.
c) Describe the operation of the circuit.
Exercise 7: Memory circuit and speed control of a cylinder
The Problem
A double acting cylinder pushes products from a magazine onto a chute. The cylinder is to extend fully when a push-button is operated. The cylinder is not to retract until full extension is reached. Extension is confirmed by a roller lever valve. The cylinder is to continue forward even if the push-button is released before full extension is reached. The speed of the cylinder is to be adjustable in both directions
of motion.
FIG. Exercise 7
Exercise
a) Draw the circuit diagram for the problem.
b) Designate the valves and indicated the numbering system for the connections.
Questions
1. What is the switching status of the memory valve when first fitted to the system and therefore what position will the cylinder be in?
2. Describe the operation of the circuit.
3. If the push-button is held operated even after full extension is reached, what effect will this have on the cylinder retraction?
4. What is the effect on the operation of fitting the roller lever valve at the mid-stroke position of the cylinder, i.e. not at the full extension position?
Exercise 8: The time delay valve
The Problem
A double acting cylinder is used to press together glued components. Upon operation of a push-button, the clamping cylinder extends and trips a roller lever valve. Once the fully extended position is reached, the cylinder is to remain for a time of T=6 seconds and then immediately retract to the initial position. A new start cycle is only possible after the cylinder has fully retracted. The cylinder extension is to be slow and the retraction adjustable but relatively fast.
FIG. Exercise 8
Exercise
a) Draw the circuit diagram for the problem.
b) Designate the valves and indicated the numbering system for the connections.
c) Describe the operation of the circuit.
7. 1.Industrial application of pneumatics
6.Pneumatic tutorial problems
SIMPLE PNEUMATIC CIRCUIT EXERCISES
Direct control of a pneumatic cylinder
The simplest level of control for the single or double acting cylinder involves direct control signals. Direct control is used where the flow rate required to operate the cylinder is relatively small, and the size of the control valve is also small with low actuating forces. If the valve is too large, the operating forces required may be too great for direct manual operation.
Exercise 1: Direct control of a single acting cylinder
The Problem
A single acting cylinder of 25mm diameter is to clamp a component when a push-button is pressed. As long as the push-button is activated, the cylinder is to remain in the clamped position. If the push-button is released, the clamp is to retract.
Exercise
a) Draw the circuit diagram for the problem.
b) Designate the valves and indicate the numbering system for the connections (ports).
c) Describe the operation of the circuit.
FIG. Exercise 1
Exercise 2: Direct control of a double acting cylinder
The Problem
A double acting cylinder is to extend when a push-button is operated. Upon release of the push-button the cylinder is to retract. The cylinder is of small bore (25mm diameter) requiring a small flow rate to operate at the correct speed.
Exercise
a) Draw the circuit diagram for the problem.
b) Designate the valves and indicate the numbering system for the connections (ports).
Exercise 3 : Indirect control of a single acting cylinder
The Problem
A large diameter single acting cylinder is to extend upon operation of a push-button valve. The push-button valve is situated at a remote position. Therefore indirect control should be used to operate the cylinder. The cylinder is to retract once the remote push-button is released.
FIG. Exercise 3
Exercise
a) Draw the circuit diagram for the problem.
b) Designate the valves and indicate the numbering system for the connections (ports).
c) Describe the operation of the circuit.
d) Explain why the remote positioning of a valve is advantageous
Exercise 4: Indirect control of a double acting cylinder
The Problem
A double acting cylinder is to extend when a push-button is operated. Upon release of the push-button the cylinder is to retract. The cylinder is 250mm diameter and consumes a large volume of air.
FIG. Exercise 4
Exercise
a) Draw the circuit diagram for the problem.
b) Designate the valves and indicated the numbering system for the connections.
c) Describe the operation of the circuit.
Exercise 5: The logic AND function; the two pressure valve
The Problem
A transfer station removes a product from a conveyor belt. If the product is detected as present and if the operator presses the push-button, the pick-up cylinder 1.0 extends. The product is sensed by a 3/2 way roller lever valve. Upon the release of the push-button the cylinder 1.0 is to retract to the initial position.
FIG. Exercise 5
Exercise
a) Draw the circuit diagram for the problem.
b) Designate the valves and indicated the numbering system for the connections.
c) Describe the operation of the circuit.
Exercise 6: The logic OR function; the shuttle valve
The Problem
A cylinder is used to transfer parts from a magazine. If either a push button or a foot pedal is operated, then the cylinder is to be extended. Once the cylinder is fully extended, it is to retract to the original position. A 3/2 way roller lever valve is to be used to detect the full extension of the cylinder.
FIG. Exercise 6
Exercise
a) Draw the circuit diagram for the problem.
b) Designate the valves and indicated the numbering system for the connections.
c) Describe the operation of the circuit.
Exercise 7: Memory circuit and speed control of a cylinder
The Problem
A double acting cylinder pushes products from a magazine onto a chute. The cylinder is to extend fully when a push-button is operated. The cylinder is not to retract until full extension is reached. Extension is confirmed by a roller lever valve. The cylinder is to continue forward even if the push-button is released before full extension is reached. The speed of the cylinder is to be adjustable in both directions
of motion.
FIG. Exercise 7
Exercise
a) Draw the circuit diagram for the problem.
b) Designate the valves and indicated the numbering system for the connections.
Questions
1. What is the switching status of the memory valve when first fitted to the system and therefore what position will the cylinder be in?
2. Describe the operation of the circuit.
3. If the push-button is held operated even after full extension is reached, what effect will this have on the cylinder retraction?
4. What is the effect on the operation of fitting the roller lever valve at the mid-stroke position of the cylinder, i.e. not at the full extension position?
Exercise 8: The time delay valve
The Problem
A double acting cylinder is used to press together glued components. Upon operation of a push-button, the clamping cylinder extends and trips a roller lever valve. Once the fully extended position is reached, the cylinder is to remain for a time of T=6 seconds and then immediately retract to the initial position. A new start cycle is only possible after the cylinder has fully retracted. The cylinder extension is to be slow and the retraction adjustable but relatively fast.
Exercise
a) Draw the circuit diagram for the problem.
b) Designate the valves and indicated the numbering system for the connections.
c) Describe the operation of the circuit.
SIMPLE PNEUMATIC CIRCUIT EXERCISES
Direct control of a pneumatic cylinder
The simplest level of control for the single or double acting cylinder involves direct control signals. Direct control is used where the flow rate required to operate the cylinder is relatively small, and the size of the control valve is also small with low actuating forces. If the valve is too large, the operating forces required may be too great for direct manual operation.
Exercise 1: Direct control of a single acting cylinder
The Problem
A single acting cylinder of 25mm diameter is to clamp a component when a push-button is pressed. As long as the push-button is activated, the cylinder is to remain in the clamped position. If the push-button is released, the clamp is to retract.
Exercise
a) Draw the circuit diagram for the problem.
b) Designate the valves and indicate the numbering system for the connections (ports).
c) Describe the operation of the circuit.
FIG. Exercise 1
Exercise 2: Direct control of a double acting cylinder
The Problem
A double acting cylinder is to extend when a push-button is operated. Upon release of the push-button the cylinder is to retract. The cylinder is of small bore (25mm diameter) requiring a small flow rate to operate at the correct speed.
Exercise
a) Draw the circuit diagram for the problem.
b) Designate the valves and indicate the numbering system for the connections (ports).
Exercise 3 : Indirect control of a single acting cylinder
The Problem
A large diameter single acting cylinder is to extend upon operation of a push-button valve. The push-button valve is situated at a remote position. Therefore indirect control should be used to operate the cylinder. The cylinder is to retract once the remote push-button is released.
FIG. Exercise 3
Exercise
a) Draw the circuit diagram for the problem.
b) Designate the valves and indicate the numbering system for the connections (ports).
c) Describe the operation of the circuit.
d) Explain why the remote positioning of a valve is advantageous
Exercise 4: Indirect control of a double acting cylinder
The Problem
A double acting cylinder is to extend when a push-button is operated. Upon release of the push-button the cylinder is to retract. The cylinder is 250mm diameter and consumes a large volume of air.
FIG. Exercise 4
Exercise
a) Draw the circuit diagram for the problem.
b) Designate the valves and indicated the numbering system for the connections.
c) Describe the operation of the circuit.
Exercise 5: The logic AND function; the two pressure valve
The Problem
A transfer station removes a product from a conveyor belt. If the product is detected as present and if the operator presses the push-button, the pick-up cylinder 1.0 extends. The product is sensed by a 3/2 way roller lever valve. Upon the release of the push-button the cylinder 1.0 is to retract to the initial position.
FIG. Exercise 5
Exercise
a) Draw the circuit diagram for the problem.
b) Designate the valves and indicated the numbering system for the connections.
c) Describe the operation of the circuit.
Exercise 6: The logic OR function; the shuttle valve
The Problem
A cylinder is used to transfer parts from a magazine. If either a push button or a foot pedal is operated, then the cylinder is to be extended. Once the cylinder is fully extended, it is to retract to the original position. A 3/2 way roller lever valve is to be used to detect the full extension of the cylinder.
FIG. Exercise 6
Exercise
a) Draw the circuit diagram for the problem.
b) Designate the valves and indicated the numbering system for the connections.
c) Describe the operation of the circuit.
Exercise 7: Memory circuit and speed control of a cylinder
The Problem
A double acting cylinder pushes products from a magazine onto a chute. The cylinder is to extend fully when a push-button is operated. The cylinder is not to retract until full extension is reached. Extension is confirmed by a roller lever valve. The cylinder is to continue forward even if the push-button is released before full extension is reached. The speed of the cylinder is to be adjustable in both directions
of motion.
FIG. Exercise 7
Exercise
a) Draw the circuit diagram for the problem.
b) Designate the valves and indicated the numbering system for the connections.
Questions
1. What is the switching status of the memory valve when first fitted to the system and therefore what position will the cylinder be in?
2. Describe the operation of the circuit.
3. If the push-button is held operated even after full extension is reached, what effect will this have on the cylinder retraction?
4. What is the effect on the operation of fitting the roller lever valve at the mid-stroke position of the cylinder, i.e. not at the full extension position?
Exercise 8: The time delay valve
The Problem
A double acting cylinder is used to press together glued components. Upon operation of a push-button, the clamping cylinder extends and trips a roller lever valve. Once the fully extended position is reached, the cylinder is to remain for a time of T=6 seconds and then immediately retract to the initial position. A new start cycle is only possible after the cylinder has fully retracted. The cylinder extension is to be slow and the retraction adjustable but relatively fast.
Exercise
a) Draw the circuit diagram for the problem.
b) Designate the valves and indicated the numbering system for the connections.
c) Describe the operation of the circuit.
7. 1.Industrial application of pneumatics